2017 Excellence in Environmental Engineering and Science® Awards Competition Winner
Superior Achievement in Environmental Engineering and Science
Category Entered: Industrial Waste Practice
The Evolution of STAR from Laboratory Concept to Full-Scale In Situ Implementation
Entrant: Savron, A Division of Geosyntec Consultants, Inc. Engineer in Charge: Scott Drew, LSRP Location: Newark, New Jersey Media Contact: David Major, Ph.D., BCES, Managing Director, Savron
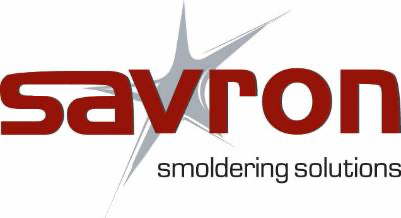
Entrant Profile
Savron is an operating division of Geosyntec Consultants International, Inc., an employee- owned, multi-national provider of sustainable waste management and remediation solutions, specializing in the safe, energy-efficient, environmentally responsible treatment of a broad range of hazardous materials. Savron helps organizations in the oil and gas, waste management, chemical manufacturing, and utilities industries manage environmental liabilities and comply with regulatory requirements.
Self-sustaining treatment for active remediation (STAR) is based on patented technology – an energy-efficient self-sustaining combustion process that captures and recycles the energy released from hazardous materials to destroy them in an effective, controllable, and safe manner. A broad range of hazardous materials including petroleum hydrocarbons, coal tar, creosote, mineral oils, and solvents can be treated by this technology. It works faster and to a dramatically higher environmental standard than common hazardous waste disposal practices such as thermal desorption, incineration, solidification, or landfilling.
A committed team of individuals from Savron, Geosyntec, the University of Western Ontario, Queensland University, and Strathclyde University successfully took the initial laboratory concept of STAR through three rounds of pilot scale demonstrations of the technology, garnered its acceptance by the New Jersey Department of Environmental Protection (NJDEP) as the selected remedy of choice by the client, to its current full-scale implementation at a former manufacturing facility impacted by coal tar in Newark, New Jersey. The full-scale remedy began in November 2014 and is anticipated to be complete by mid-year of 2018.
Project Description
Background
This 26-acre former coal tar processing facility is located in Newark, New Jersey (NJ). The project objective is to obtain a no-further action letter from NJDEP as part of a land transaction agreement. This requires the removal of the mobile non-aqueous phase liquid (NAPL) coal tars to the "extent practicable".
STAR is a patented self-sustaining process based on the principals of smoldering combustion to destroy heavy hydrocarbons. Although laboratory treatability studies showed that STAR could effectively treat the contaminated soils, this technology had not been demonstrated to work under field conditions, and particularly below the water table. Pilot testing: (1) demonstrated smoldering under field conditions; (2) allowed for the development of STAR equipment; and (3) provided data for full-scale design and costing. Key design data collected included the smoldering front propagation rate and radius of influence (ROI), and emission profiles (off-gas treatment requirement).
As shown by Scholes et al (2015), the pilot tests demonstrated that a single ignition point resulted in over 5,000 kilograms of coal tar destroyed within two-weeks to target a depth of approximately 9 meters (m) below the ground surface, with concentrations reductions of three to four orders of magnitude below criteria.
Feasibilities studies indicated that the cost of a STAR remedy would be at least 50% less than competing remedial alternatives (in situ stabilization, excavation with off-site thermal treatment), while also having 1/10th the carbon footprint.
Implementation of STAR under NJ's Licensed Site Remediation Professional (LSRP) program began in November 2014 (beginning of procurement, site preparation and mobilization) and is to be complete by mid-2018.
Integrated Approach to Environmental Media
Acceptance of the full-scale application of STAR by the client and regulatory agency was contingent on effectively addressing all the impacted media and meeting the following remedial action objectives (RAOs):
- Protection of people and the environment;
- treat "mobile" NAPL to the extent practicable;
- management of direct contact risks;
- reduce impacts to facilitate the use of monitored natural attenuation remedy for groundwater; and
- compliance with applicable regulations.
The Remedial Action Work Plan (RAWP) addressed the above RAO and:
- all emission permits (recuperative thermal oxidizer), soil management, and abandoned underground utilities;
- delivery and/or management of fixed and mobile energy to the site; and
- The identification and protection of any potential receptors.
Quality
The mass of coal tar destroyed and the removal of mobile NAPL to the extent practicable as per the NJ Technical Regulations demonstrated the quality and performance of STAR.
Continuous emission monitoring of combustion gasses showed conservatively the destruction of over 20 metric tons of coal tar within approximately 5,500 cubic yards of treated soil to date. Over 90% of the 137 samples taken within the treated area had an average extractable petroleum hydrocarbon (NJDEP EPH method) concentration of 3,378 mg/kg (standard deviation of 4,438 mg/kg). This is significantly below the 17,000 mg/kg value used as default value for the presence of mobile NAPL in soil samples, indicating NAPL removal to the extent practicable. STAR may be re-deployed to areas where remedy verification targets were not met.
Finally, the testimonial letter shows that our client is extremely pleased with our efforts to solve one of their most complex sites.
Contributions to Social and Economic Advancement
The development of the Pitt Consol property will be one step in the re-vitalization of the Newark Ironbound district. This area was heavily industrialized and as it is transformed it will generate new jobs and new opportunities locally and nationally. The transition from manufacturing to commercial space recognizes the advancement being made and the successful maturation of the global economy. Rather than use agricultural land for new developments the parties involved are working together to re-use land through sustainable means.
Originality and Innovation
Taking a never field-tested, laboratory scale process and making it real required originality and innovation. We developed practical, deployable, effective heaters that provide sufficient energy to initiate an exothermic, self-sustaining smolder reaction under flowing water conditions. Publication of our work in Environmental Science and Engineering Journal indicates our originality and innovation.
Another challenge was reducing our uncertainty regarding NAPL distribution to estimate the number and location of ignition points. We achieved this through developing a sampling grid strategy that optimized the use of TarGOST™ (a push tool that uses a laser to induce fluorescence of coal tar constituents). EVS software was used to evaluate the TarGOST data to develop an unprecedented level of understanding of the NAPL 3D distribution.
Our full-scale remedy included construction of unique integrated equipment to manage air injection and extraction (at over 3,000 standard cubic feet per minute), mobile and stationary power, downhole heater control, management and measurement of combustion gases, monitoring of in situ combustion temperatures, and vapor collection with emission treatment and monitoring.
Complexity
A complex problem is the need to use 2,150 ignition points spaced horizontally and at multiple depths over a wide area. To avoid the costs associated with installing all these wells and infrastructure, we developed an innovative "leapfrog" approach. The site was divided into 200 ft radius "nodes" that could be serviced by a mobile treatment trailer. The trailer contained the air distribution/extraction manifold system, electrical distribution, continuous monitoring systems, and heater controls. Ignition wells are divided into cells, with three cells active per treatment plant. One cell would be actively operated (air injection), wells in a completed cell would be extracted for reuse, and ignition wells would be installed in another cell. This results in approximately 70 wells being either operated, demobilized for reuse, or being installed in each node.
Vapor capture and treatment was achieved through shallow extraction wells placed through a preinstalled asphalt cap. Collected emissions are continuously monitored for combustion gasses to verify smoldering/estimate mass destroyed, and treated via recuperative thermal oxidizer. Data from thermocouple probes are used to verify smolder front migration. System performance can be monitored and key systems controlled remotely. The entire system has safety interlocks and controls through a PLC.
Associated with the application of STAR, there are on-going groundwater studies. Monitored Natural Attenuation will be applicable as a groundwater remedy and final polishing step following removal of NAPL.
Click images to enlarge in separate window.
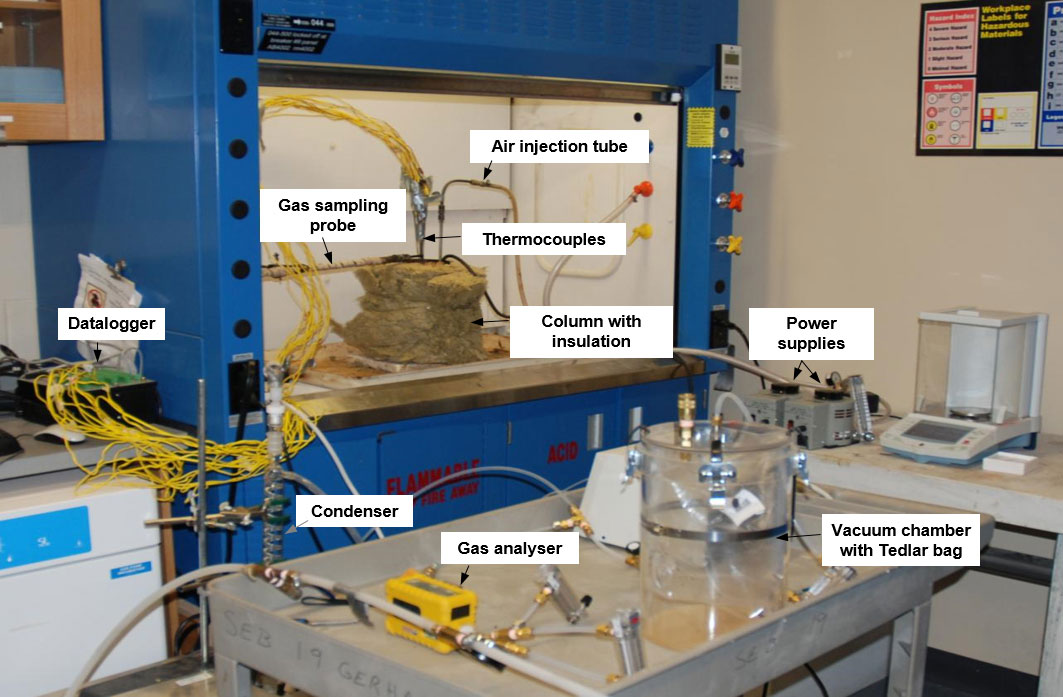 |
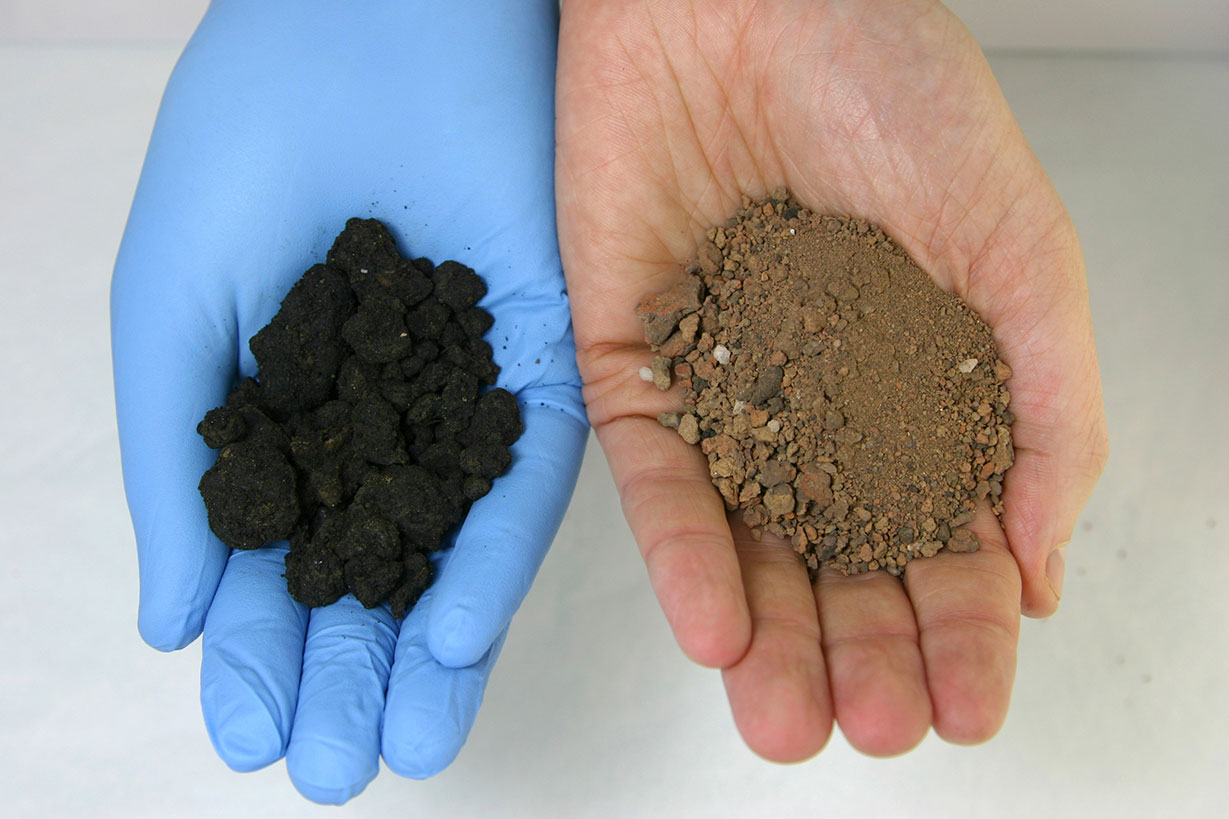 |
Column Treatability Study. Simple column tests were used to demonstrate that contaminants in the site soils could support self-sustaining smoldering reactions. A conductive heater is imbedded in clean sand above a diffuser plate. Contaminated soil is placed above the sand and instrumented with thermocouples. After a short heating period to initiate smoldering, the heater is turned off while air supply is maintained. The energy in the coal tar provides all the energy needed to maintain self-sustaining combustion reaction.
|
Treated Soils. A comparison of site soils before (left) and after (right) the laboratory treatability study. Prior to STAR, the soils are oily, black and clumpy with high TPH values (over 20,000 mg/kg). After treatment, the soils are dry and sandy. TPH values are typically non-detect.
|
>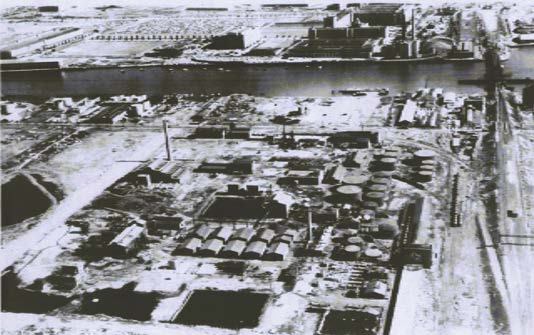 |
Site in 1954. The Site is a former chemical production and coal tar processing facility, which produced picric, acid, road and roofing tar, cresols, phenols, naphthalene and other derivatives. Operations began in approximately 1862. All production processes ceased in 1983 and by 1986 production facilities were dismantled. Lagoons located on the west and north boundaries (respectively, bottom and right of the photo), and in the center of the site, along with spills associated with the tank farms, are the suspected sources for the soil and groundwater contamination.
|
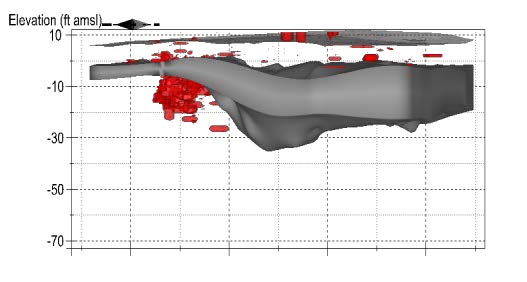 |
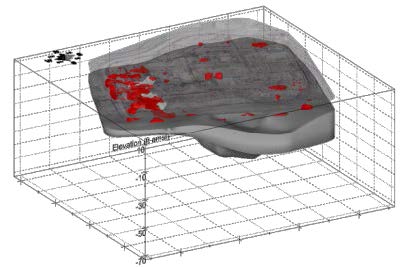 |
TarGOST. Using TarGOST data and EVS modeling, an unprecedented level of characterization of the mobile NAPL phase (shown in red) was possible. This detail allowed design of the placement of 2,300 ignition points. Much of the NAPL mass is located below where the lagoons were located. The grey zone between ca. 5 feet to -33 ft above mean seal level is a low permeable clay peat layer know locally as the "Meadow Mat".
|
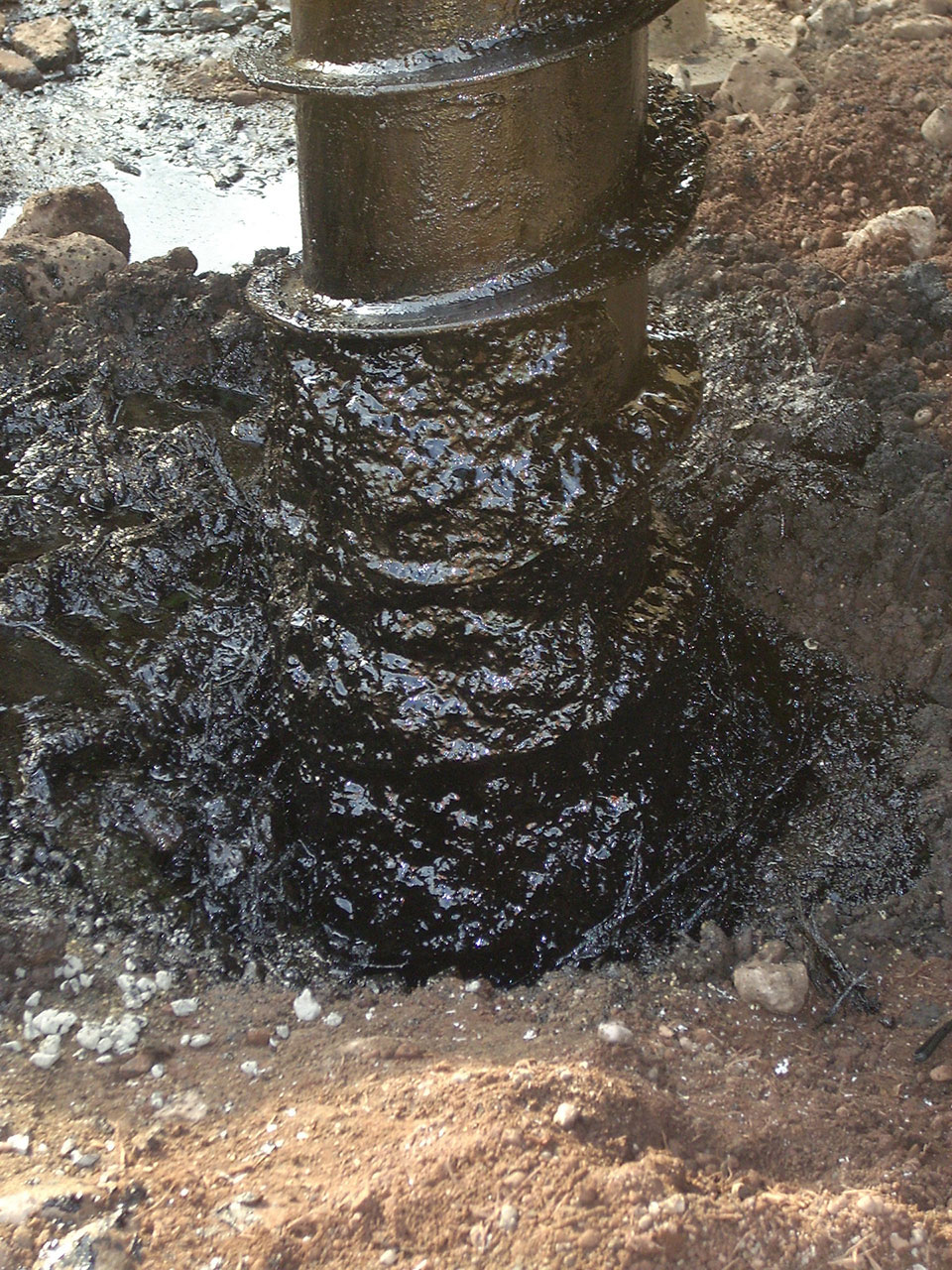 |
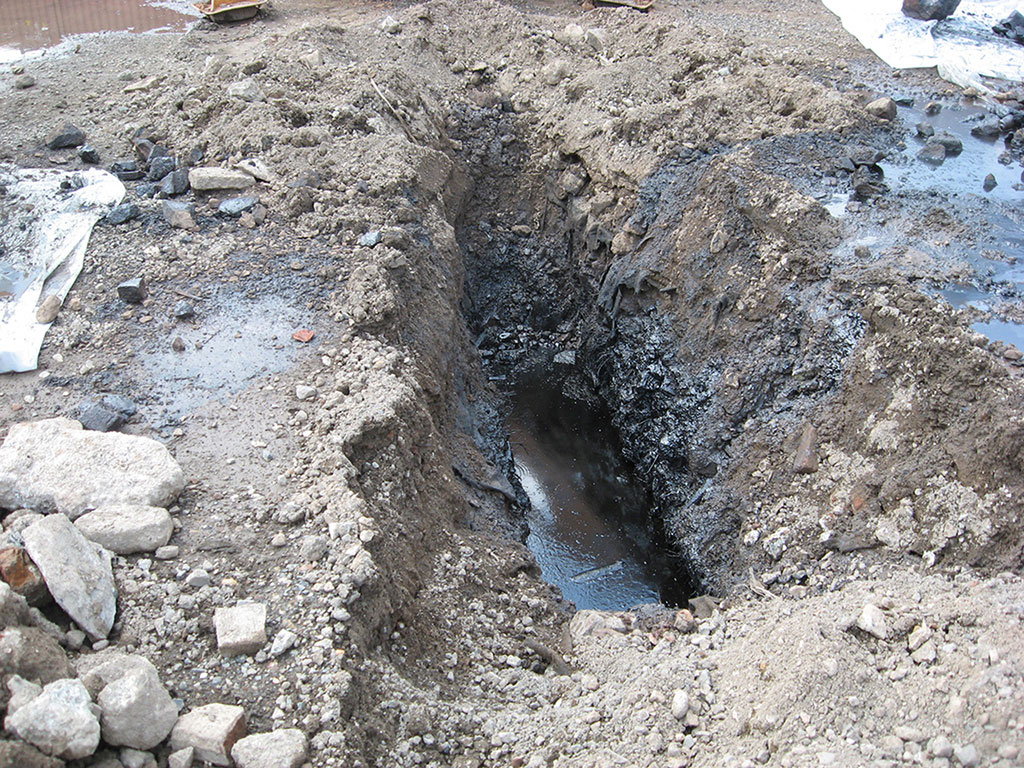 |
Pilot Test Installation. The extent of contamination is evident during installation of wells and use of test pits.
|
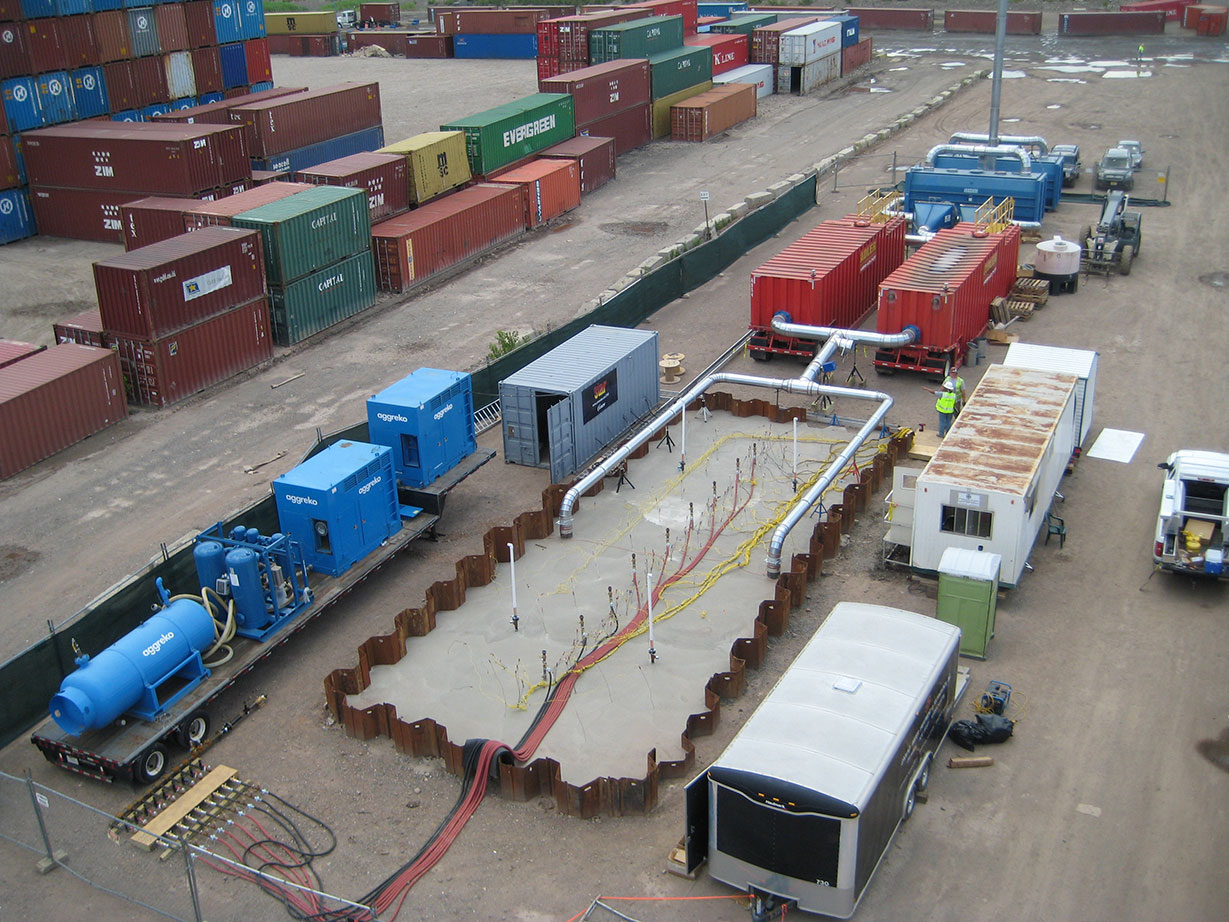 |
Proof of Concept Pilot Test. Sheet pilling was used to isolate the test area and prevent mobile coal tar from re-entering the treated soils. A gravel layer was placed on top of the soil, and capped with concrete. The sheet pile, and cap allowed complete capture of gases and allowed for better mass balance estimates. Nine ignition wells are in the center of the test cell. Red lines are for air injection, yellow are for thermocouples. Due to the many unknowns for this test, much of the equipment is oversized (air injection/ extraction, and vapor treatment).
|
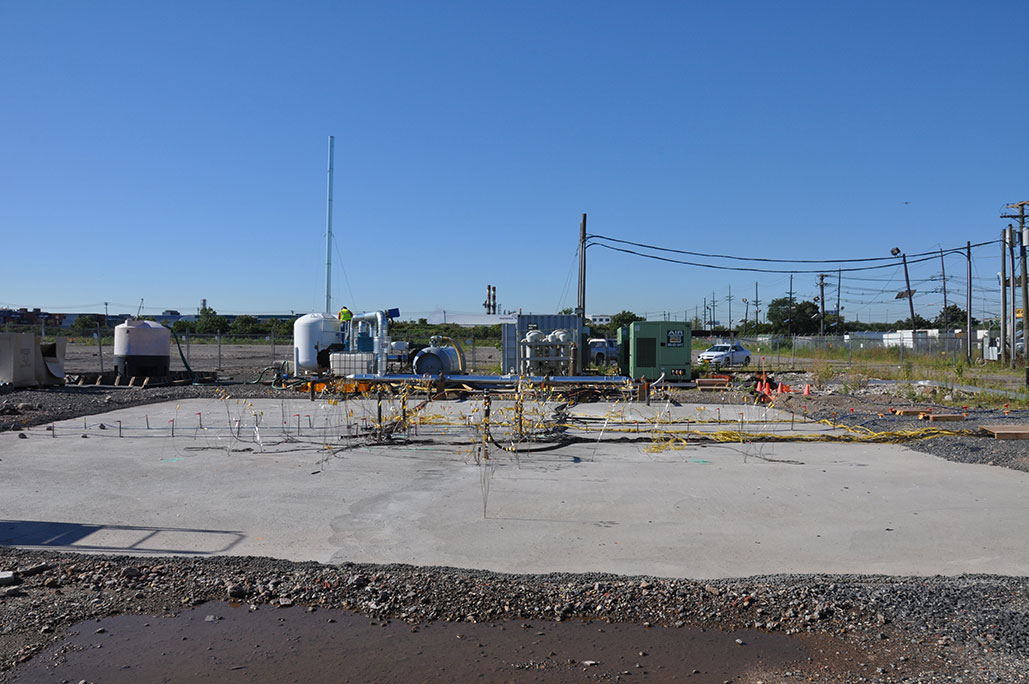 |
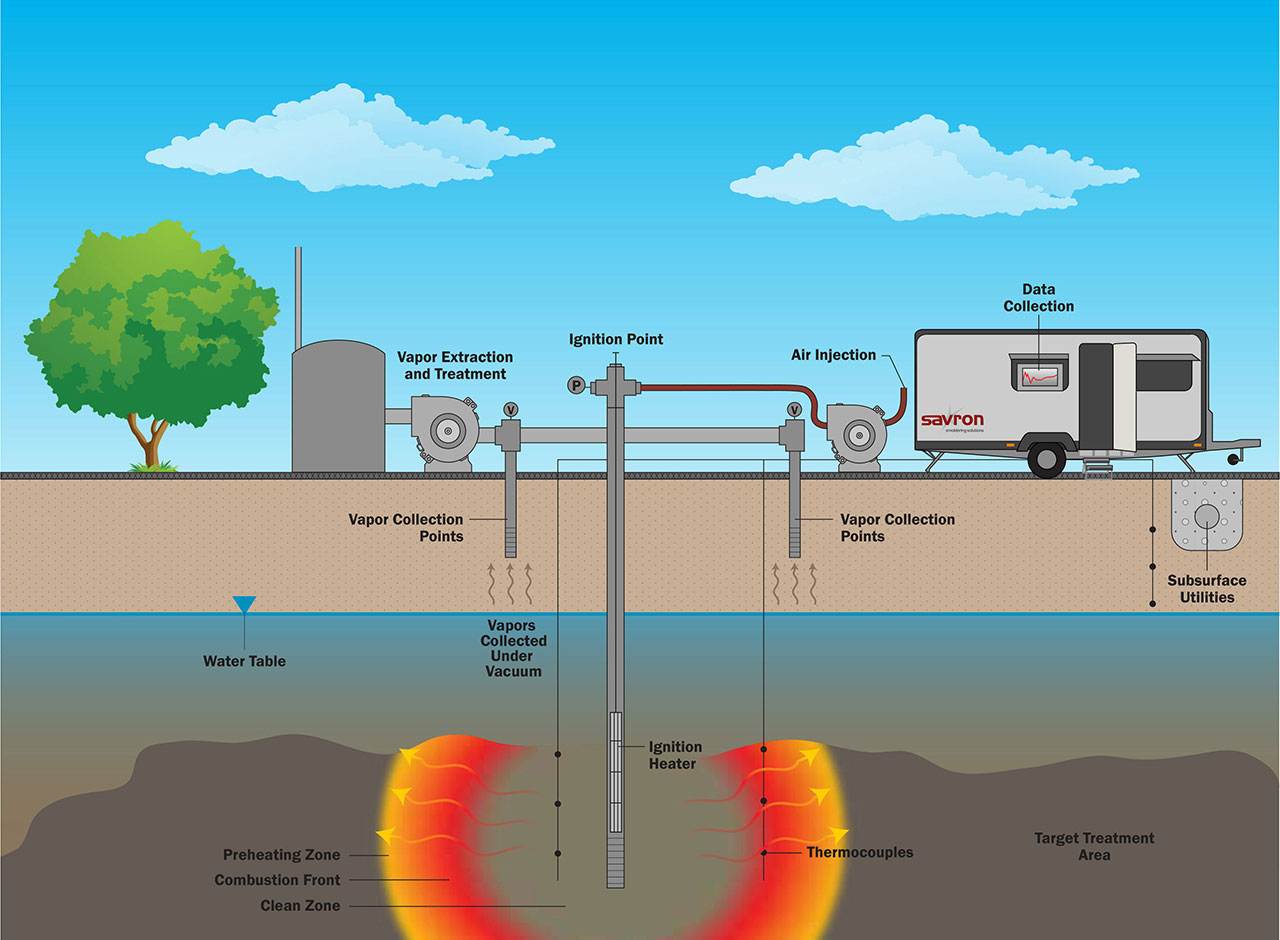 |
Final Pilot Testing. Pilot testing was conducted within the shallow and deep contaminated zones to collect key design data (radius of influence, propagation rate of the smoldering front). Note that compared to the proof of concept pilot test, there is no sheet piling (testing under natural groundwater flow conditions) and smaller equipment size.
|
Schematic of Full Scale. A 2-inch ignition point (IP) with a 6 to 12-inch stainless steel slotted screen is installed at the target depth. An in-well specially designed cartridge heater is inserted in the well and heated for a short period (2 to 12 hours) to initiate combustion. Air is injected into the IP and combustion gases are extracted under vacuum, monitored and then treated. Thermocouples are used to verify combustion temperatures (upwards of 1200°C). As the combustion front moves out, it leaves behind cool and dry soil, even under the water table.
|
 |
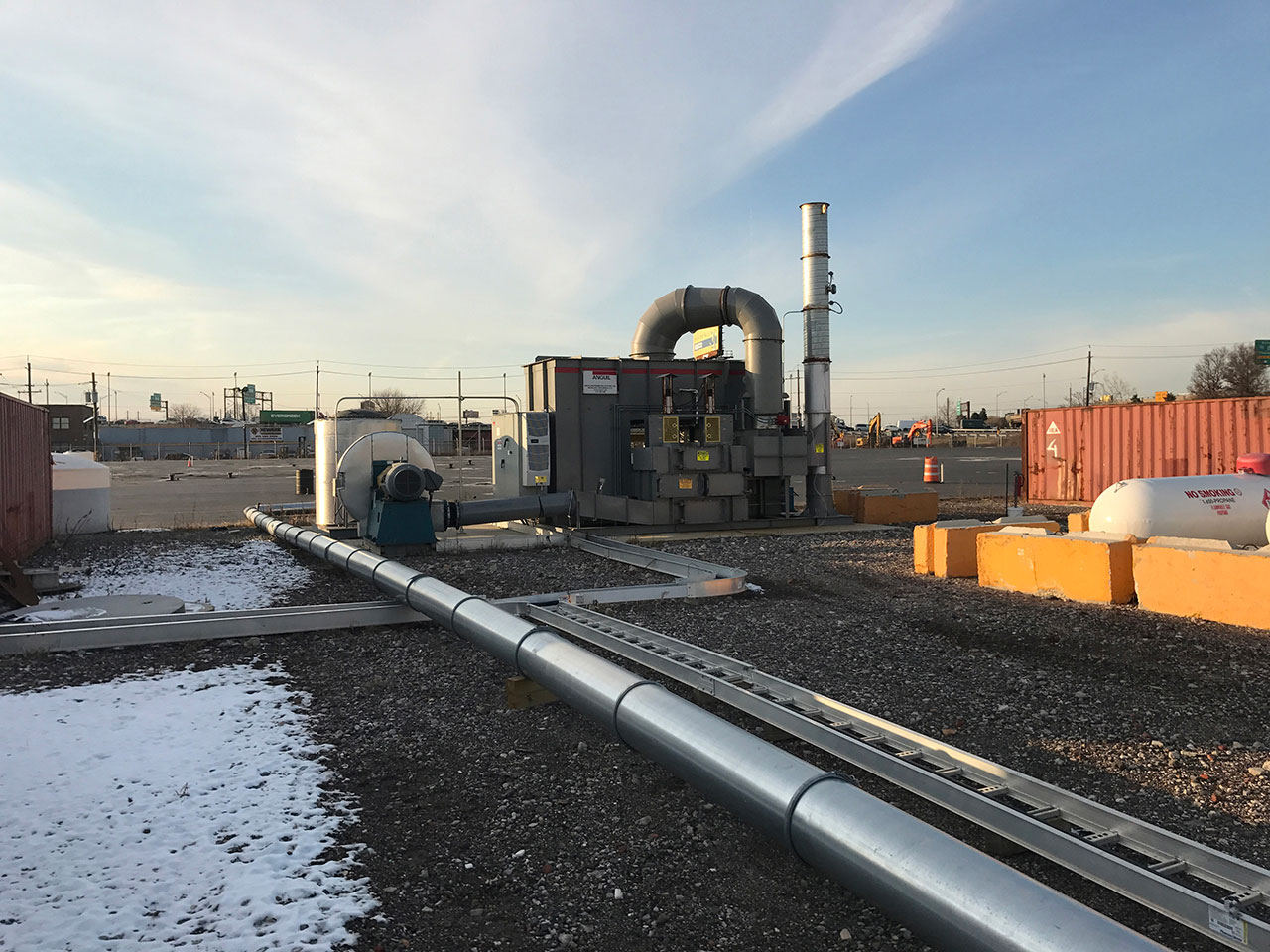 |
Mobile Treatment Trailer. The trailers manage air injection and extraction, contain the continuous emission monitoring system to continually measure concentrations of combustion gases, and provide power distribution and controls for the heaters. Each trailer could support treatment areas within a 200-foot radius. The orange tubes are the vapor extraction lines.
|
Emission Treatment. All emissions were routed to one of two recuperative thermal oxidizers (RTO). The primary purpose of the RTO was to remove carbon monoxide, as well as any low molecular weight hydrocarbons that are generated during the smoldering reaction (e.g., benzene, naphthalene, methane).
|
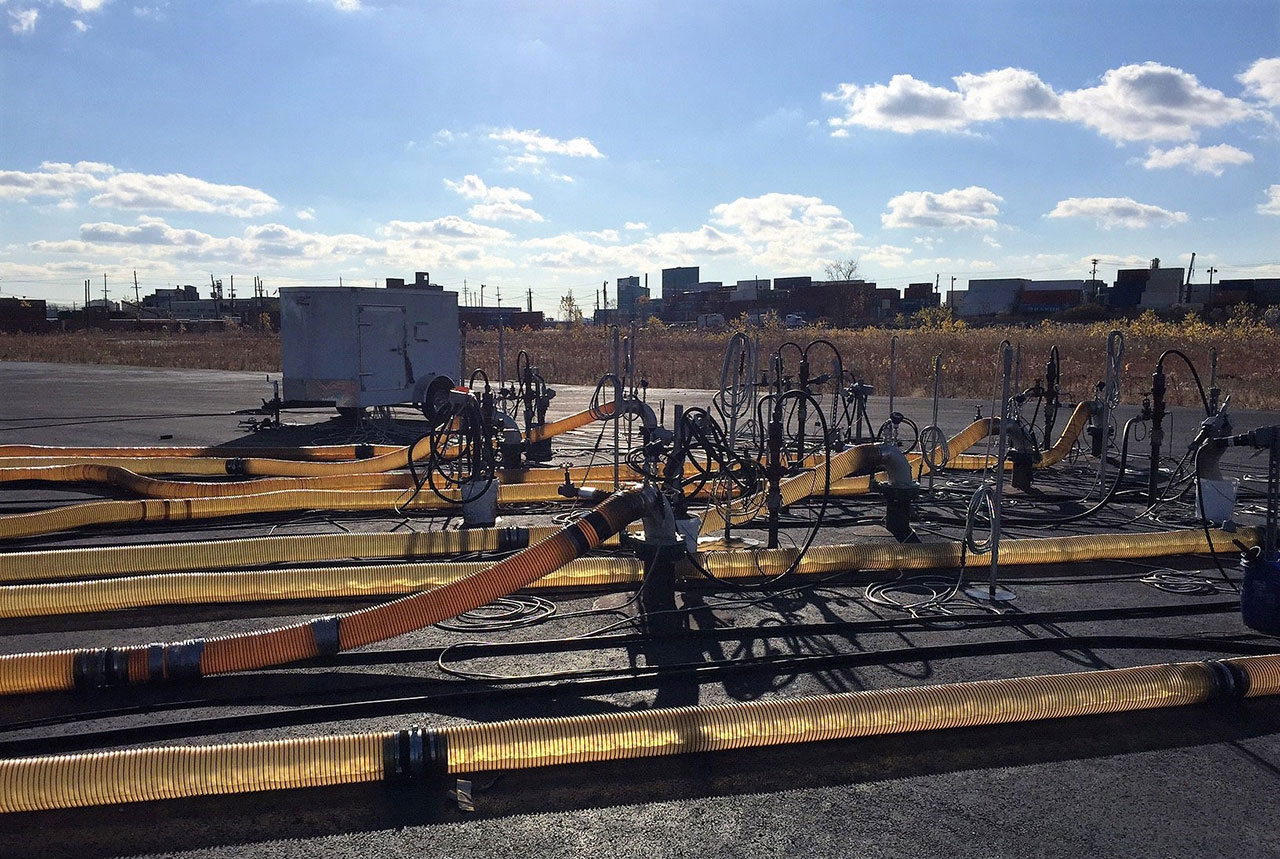 |
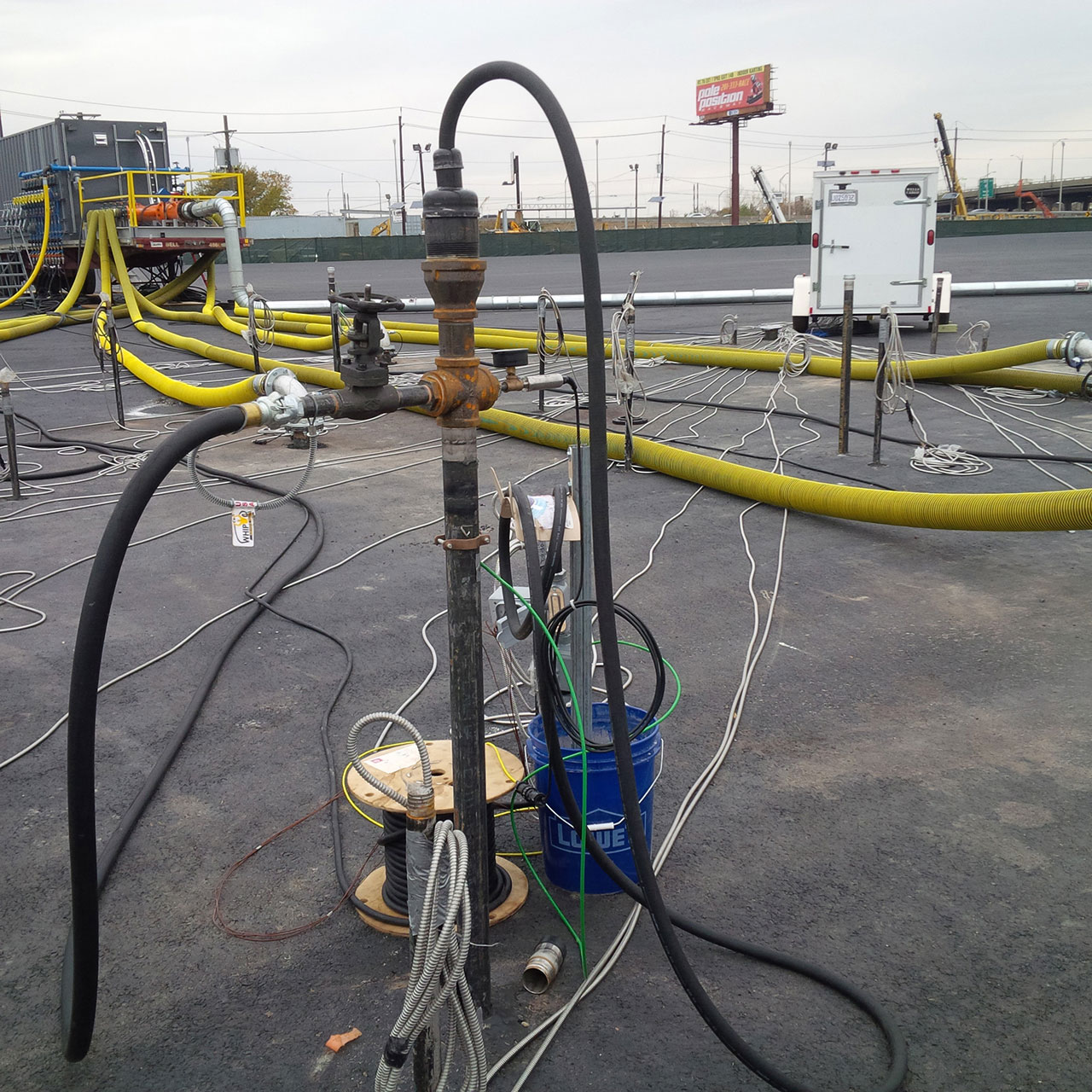 |
Treatment Cell. The site was divided into nodes and cells. A node could be serviced by one mobile trailer. A cell would be composed of operating IPs, IPs being installed, or IPsbeing removed. This picture shows an operating cell with vapor extraction points (orange lines) with IPs (dark color) and thermocouples (grey stick ups). A deep cell would have 6 operating IPs, a shallow cell up to 10 IPs'. Cells covered a treatment area approximately 40 by 60 feet at a time.
|
Ignition Point. This picture shows a close-up of an IP. Air is provided by the black line on the left, power to the heater is at the top. A pressure transducer is located on the right across from the air injection line. Vapor extraction lines are seen in the background towards the treatment trailer. Thermocouple wires (grey) are connected to a mobile data collection trailer.
|
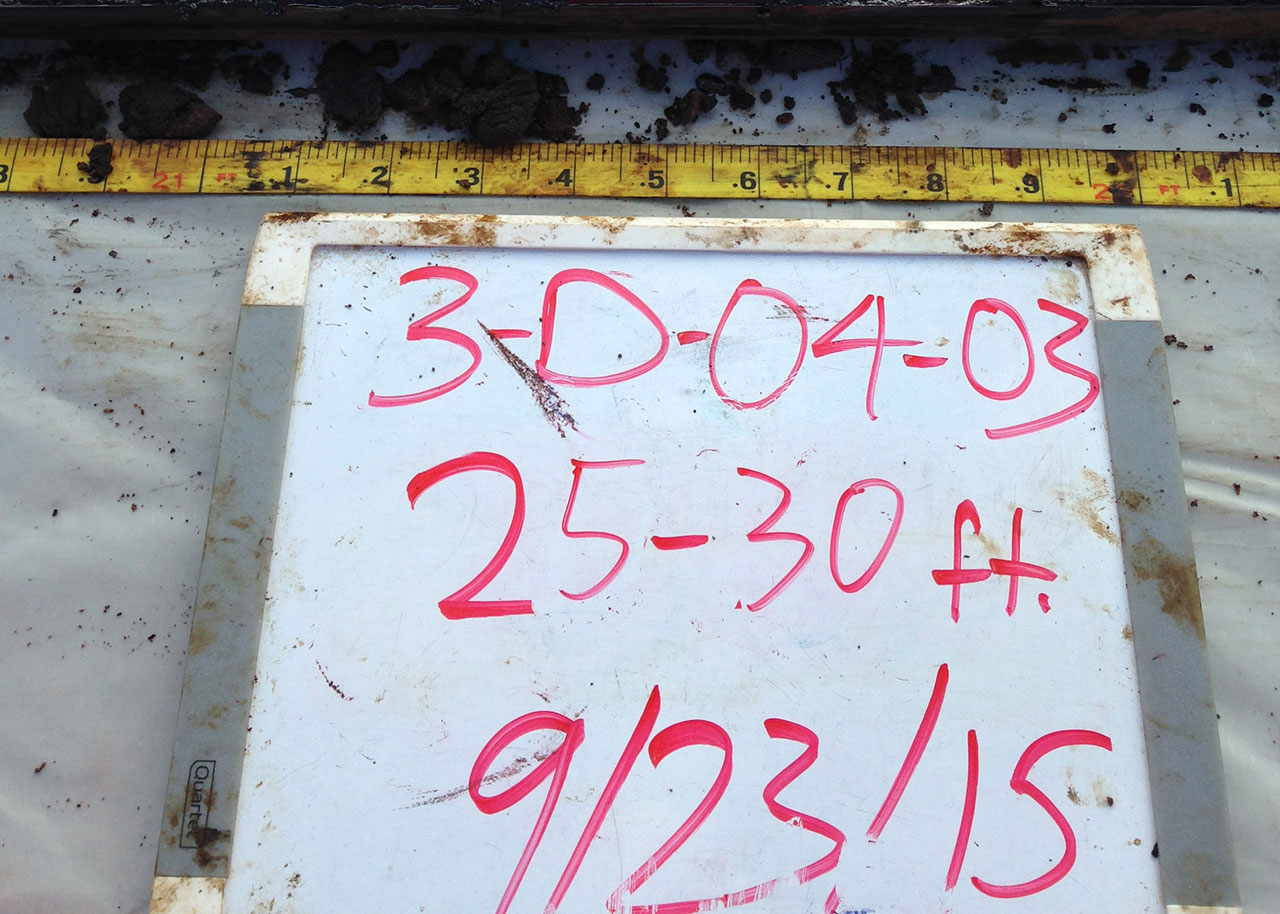 |
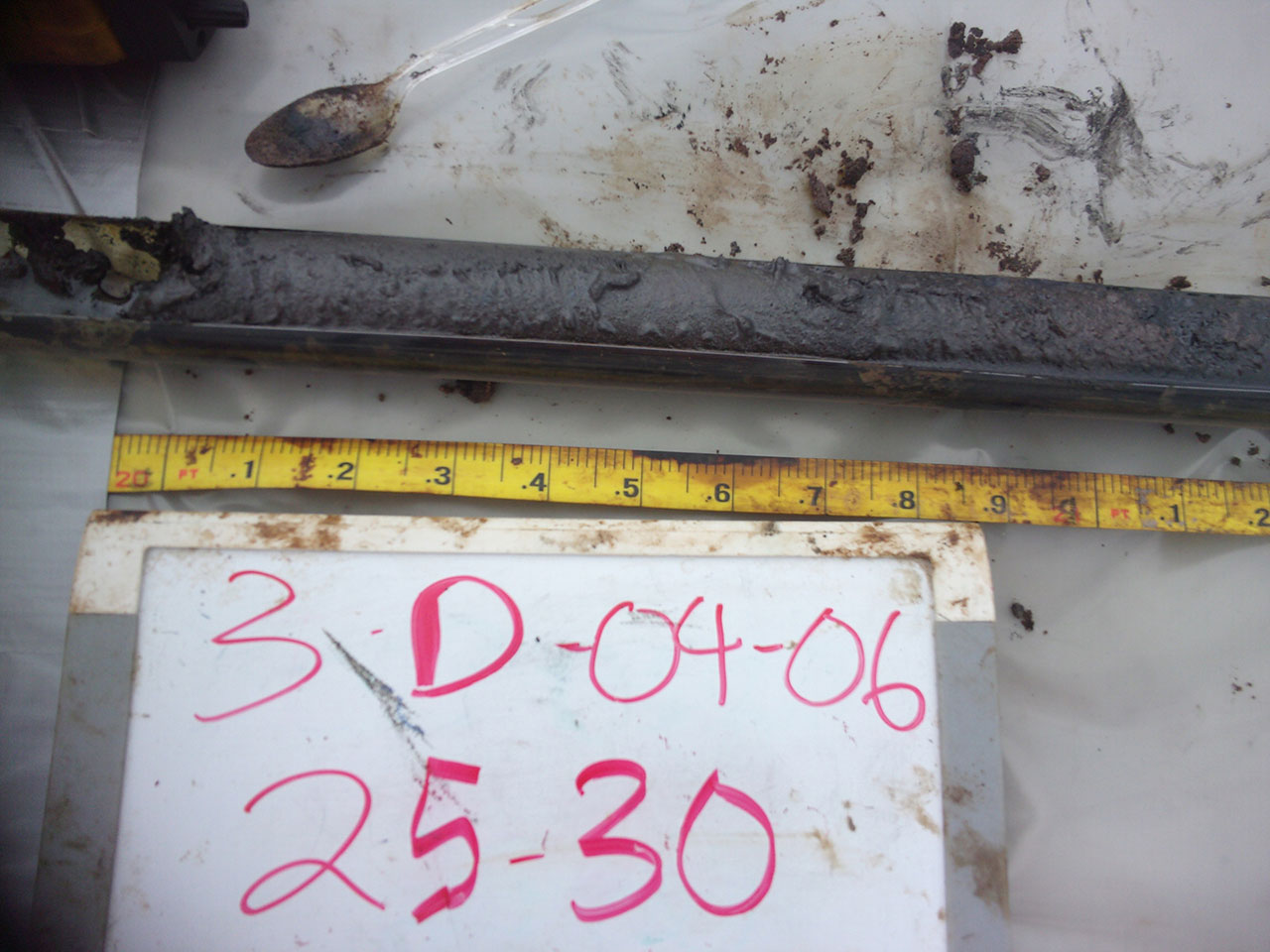 |
Pre Treatment
|
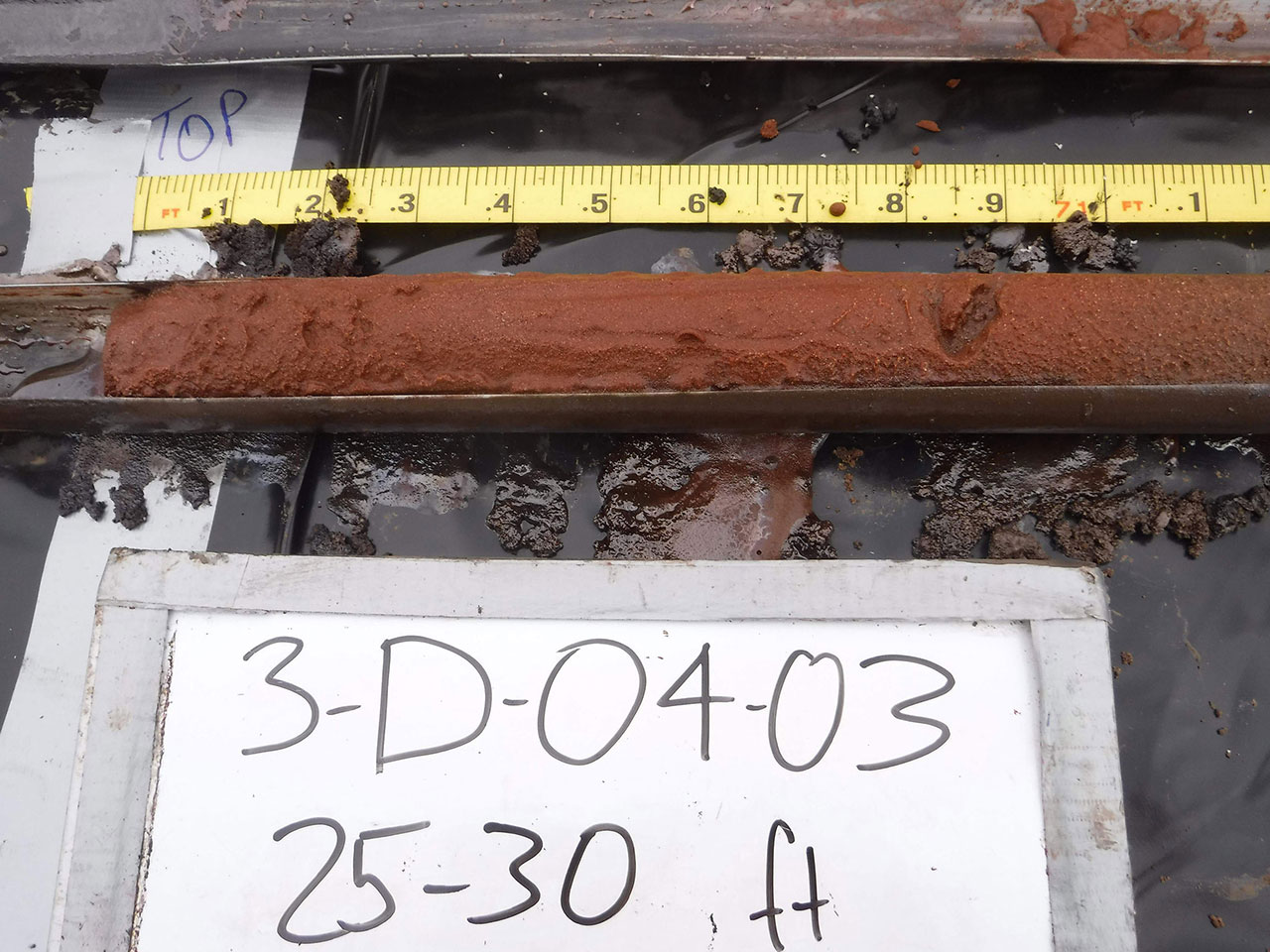 |
 |
Post Treatment
|
Treatment Effectiveness. These photographs show before and after pictures of core samples collected from a deep treatment cell at a depth of 25 - 30 feet below ground surface. The top two photos clearly show the obvious heavy contaminated sands in the aquifer. The bottom 2 photos show soils that are completely treated. The reddish colour is due to oxidation of iron minerals in the sand.
|
|