2020 Excellence in Environmental Engineering and Science® Awards Competition Winner
Superior Achievement and Grand Prize for 50th Anniversary of the 1970 Clean Air Act
Category Entered: Environmental Sustainability
Entrant: Sanitation Districts of Los Angeles County Engineer in Charge: Robert C. Ferrante, P.E., BCEE Location: Kings County, California Media Contact: Wendy Wert, P.E., BCEE
Entrant Profile
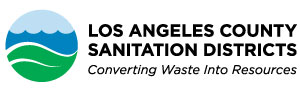
Sanitation Districts of Los Angeles County
The Sanitation Districts of Los Angeles County (Sanitation Districts) protect public health and the environment through innovative and cost-effective wastewater and solid waste management and, in doing so, convert waste into resources such as recycled water, energy, and recycled materials.
The Sanitation Districts consist of 24 independent special districts serving more than 5.6 million people in Los Angeles County. The agency's service area covers 850 square miles and encompasses 78 cities and unincorporated areas in the county. The Sanitation Districts' wastewater system treats about 390 million gallons of wastewater (sewage) per day. The Sanitation Districts' sewerage system includes 11 wastewater treatment plants, 48 pumping stations, and over 1,400 miles of sewer. The system also includes two state-of-the-art composting facilities (Tulare Lake Compost and Inland Empire Regional Composting Facility) for managing the solids removed during wastewater treatment.
The recycled water produced by our treatment plants is beneficially reused at more than 950 sites, including groundwater recharge basins, schoolyards, nurseries, parks, and farmlands. The solids removed during wastewater treatment are anaerobically digested and dewatered to produce about 500,000 tons of biosolids per year. The biosolids are beneficially used in several ways, including as soil amendment for agriculture and in creation of exceptional quality compost. Solids treatment via anerobic digestion also produces biogas, which is converted into 20 megawatts of electricity and used to maintain the temperature of the digestion process. As a result, the Sanitation Districts are one of the biggest producers of green energy.
Project Description
The Sanitation Districts of Los Angeles County (Sanitation Districts) have developed the Tulare Lake Compost (TLC) facility in Kings County, California. TLC combines agricultural and green waste from the Central Valley with biosolids from Los Angeles County to produce compost, which is applied to Sanitation Districts farmland adjacent to the composting facility or delivered to local farmers to improve crop yields and soil quality. The facility does all this while minimizing air quality impacts in an area that is not meeting air quality goals (a nonattainment zone). The facility integrates wastewater and biosolids management with soil rehabilitation, agricultural operations, and air quality improvements.
Helping the Central Valley Grow Sustainably
TLC is a composting facility that can convert up to 100,000 wet tons per year of anaerobically digested and dewatered solids into nutrient-rich compost. TLC employs an extended aerated static pile process, which forces air through a mixture of biosolids, agricultural waste, and green waste to provide oxygen for microbial decomposition. A biofilter comprised of finished compost produced at the facility is placed over the mixture to reduce emissions from the composting process and thereby improve regional air quality.
TLC produces compost that when incorporated into farmland in the San Joaquin Valley, improves water retention, nutrient conditions, and agricultural productivity. Greater water retention translates into reduced irrigation demand, conserving water. The finished product complies with EPA Part 503 standards for Class A Exceptional Quality compost and can be used for vegetable gardening and landscaping, as well as commercial agriculture.
The TLC Process Protects the Environment
Class A Exceptional Quality Compost is produced with the following four-step TLC process:
- Hauling: Natural-gas-fueled trucks arrive at the facility with biosolids, agricultural waste and green waste. The latter two materials add carbon needed for the composting process.
- Mixing: Biosolids are unloaded inside the Mixing and Receiving Building. Agricultural waste and green waste are delivered and temporarily stored outdoors. The biosolids, agricultural waste and green waste are blended using stationary mixers located inside the Mixing and Receiving Building or a specialized mixer truck.
- Composting: The blended material is laid out in piles, covered with a biofilter comprised of finished compost, and broken down by the activity of tiny microbes. The composting area is equipped with a positively aerated system, wireless temperature monitoring devices, and an irrigation system to provide moisture to the biofilter layer. This system creates ideal composting conditions within the pile, while efficiently removing odors and other emissions such as dust, ammonia, and volatile organic compounds.
- Screening: After the composting process is complete, the composted material is screened to produce a high quality and consistent product. Materials too large to pass through the screen are returned to the composting process.
Closing the Loop
Composting at TLC helps California recycle nutrients that are useful for growing crops and reduces the need for petroleum derived fertilizers. Biosolids processed into compost reduce landfill disposal. And, composting agricultural and green waste helps meet California's diversion goals and mandates for recycling. The common practice for managing agricultural and green waste in the Central Valley was by open burning, but this practice has been phased out by the San Joaquin Valley Air Pollution Control District.
Composting is an environmentally responsible alternative for managing Central Valley's agricultural and green waste. Recycling of these materials and use of Class A Exceptional Quality compost as a soil amendment is an EPA-approved practice that benefits municipalities and the agricultural community.
Clean and Green
TLC was designed with the environment in mind. TLC's Administrative Office Building is LEED (Leadership in Energy and Environmental Design) Certified, resulting in lower energy usage.
Monitoring devices and a computer control system are used to optimize composting temperature levels. Consequently, the TLC process greatly exceeds EPA's standards – pathogens destruction occurs six times longer than required, and Vector Attraction Reduction (VAR) is double EPA's requirements.
Protecting Air and Water Resources
Every aspect of TLC has been designed to keep the valley's air clean. Natural gas trucks are used to transport feedstocks to TLC, which is the first time a public agency in California has made natural gas trucks a requirement for commercial hauling of biosolids. Natural gas trucks result in approximately 17% reduction in vehicle emissions.
The Mixing and Receiving Building is under negative pressure (vacuum) to prevent release of emissions. The building's ventilation system forces the indoor air to an outdoor biofilter, which is approximately ¾ acre in size and has a volume of 200,000 cubic feet.
Prior to composting, the biosolids, agricultural waste and green waste are mixed by either electric-powered stationary mixers or a mixer truck that exceeds the highest California Air Resources Board (CARB) on-road vehicle emissions standards.
The composting process must comply with extensive air quality permit requirements. During composting, approximately 2 feet of finished compost acts as a biofilter and provides 90% reduction in volatile organic compounds and ammonia, and a 99% retention rate of particulate matter and bacteria.
After the composting process, a trommel screen is used to separate the finished compost from larger, bulky material. Loaders and other heavy equipment used at the site are all powered by engines that meet Final Tier IV air emission requirements.
All stormwater, process water, and compost leachate at the site is recycled back into the composting process.
Attaining Sustainability
The Sanitation Districts, with TLC, have successfully pioneered an integrated biosolids management program. TLC is the only large-scale, publicly owned biosolids management facility that produces Exceptional Quality compost and owns the farmland to which it is applied. TLC has the potential to recycle up to 500,000 wet tons of biosolids and 400,000 tons of agricultural waste and green waste each year. Diverting agricultural waste from open field burning helps improve air quality in an extreme nonattainment area. This project helps lead the way in achieving more sustainable waste recycling and provides guidance to other agencies as they seek better ways to manage their waste.
Click images to enlarge in separate window.
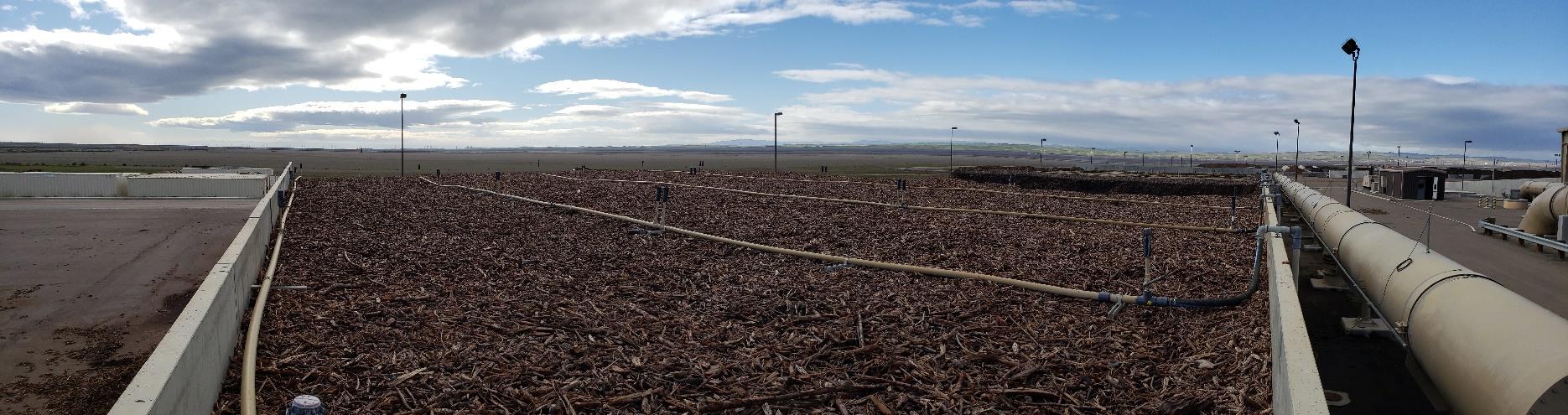 |
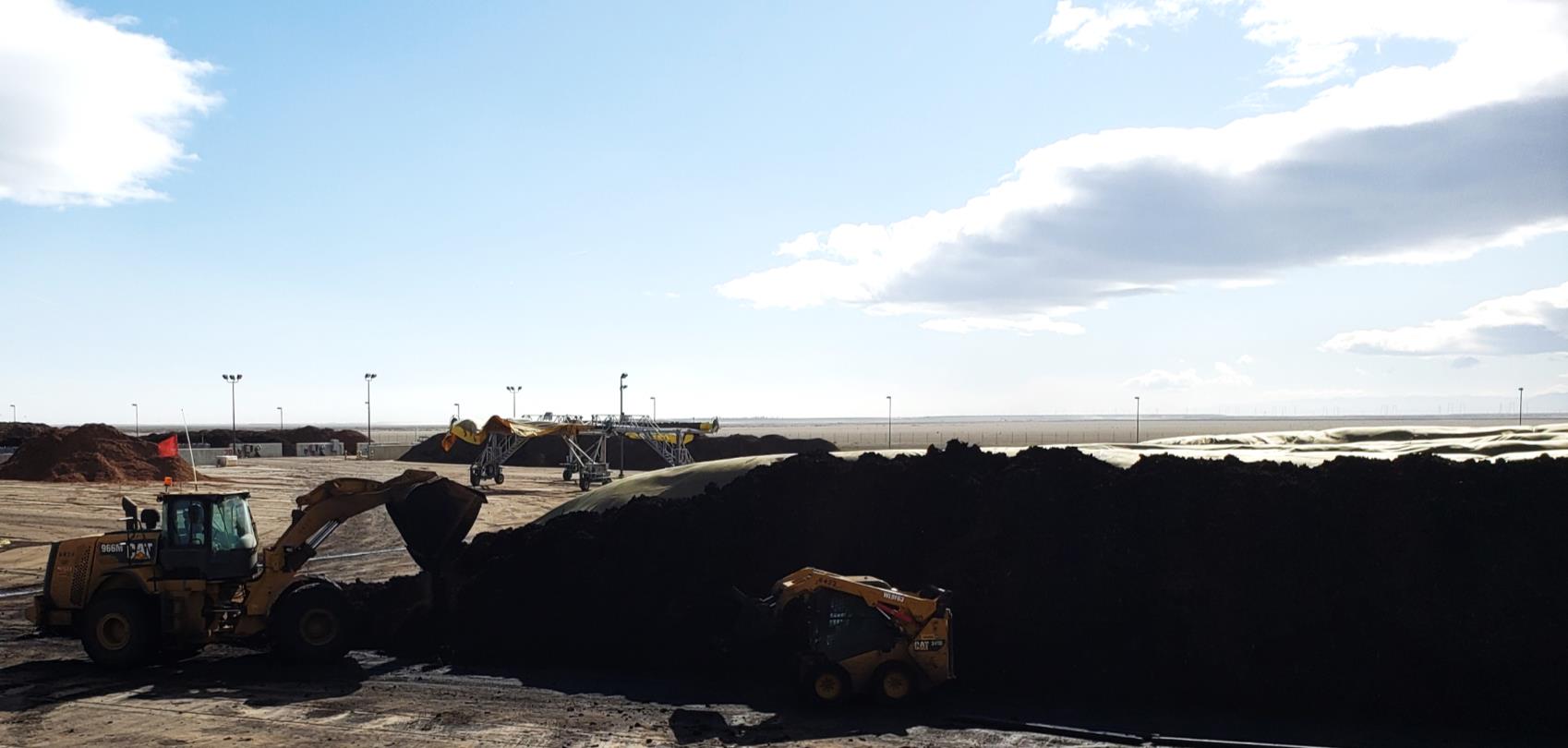 |
Biofilter wide view from Northeast corner.
|
Compost Pile being built (Loader and Skid).
|
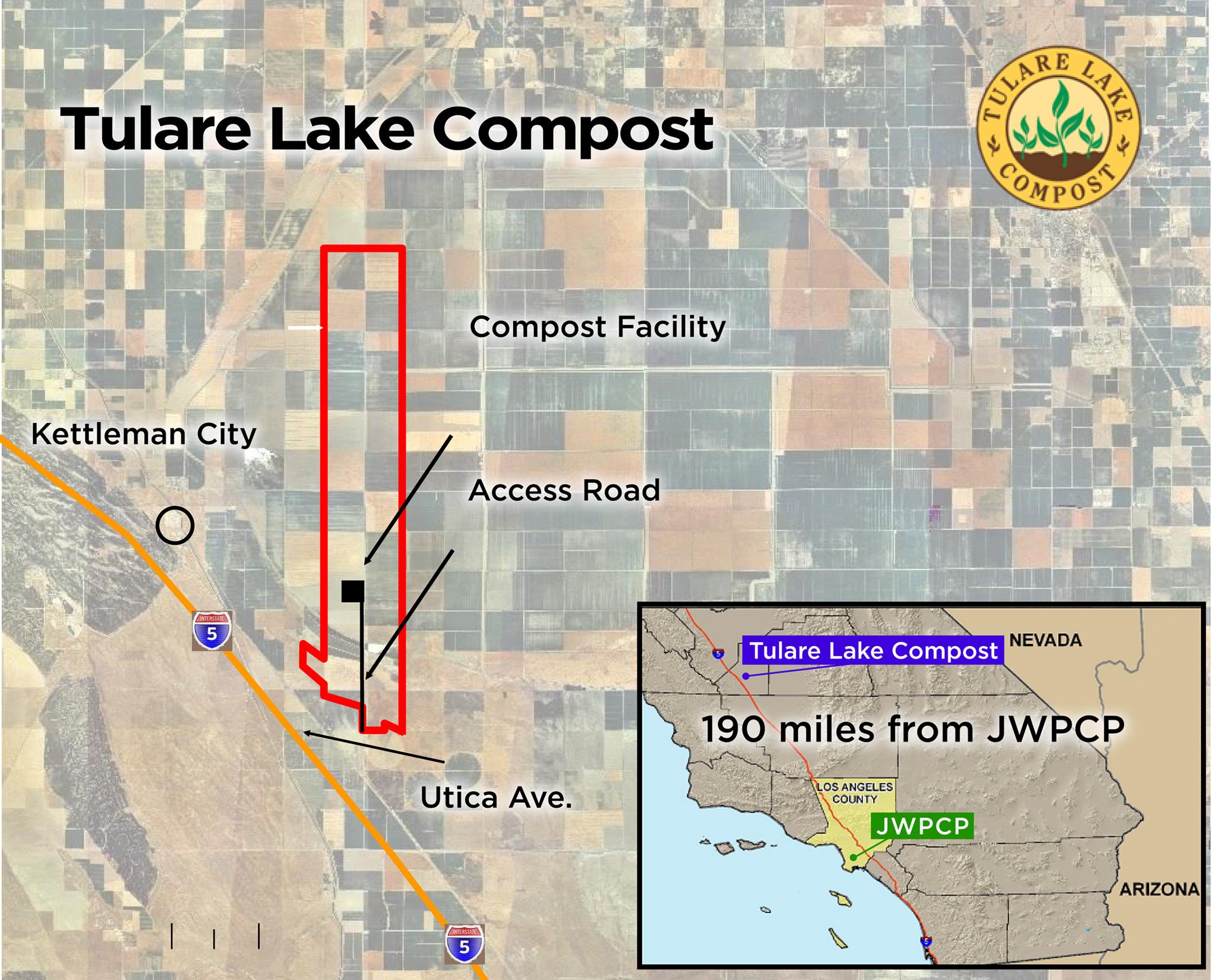 |
 |
Tulare Lake Compost, located in California's Central Valley, serves a key role in the Sanitation Districts comprehensive biosolids management program. TLC support nutrient recovery from the Sanitation Districts largest Resource Recovery Facility, the Joint Water Pollution Control Plant (JWPCP).
|
Extended Aerated Static Pile (eASP) with finished compost biofilter cover.
|
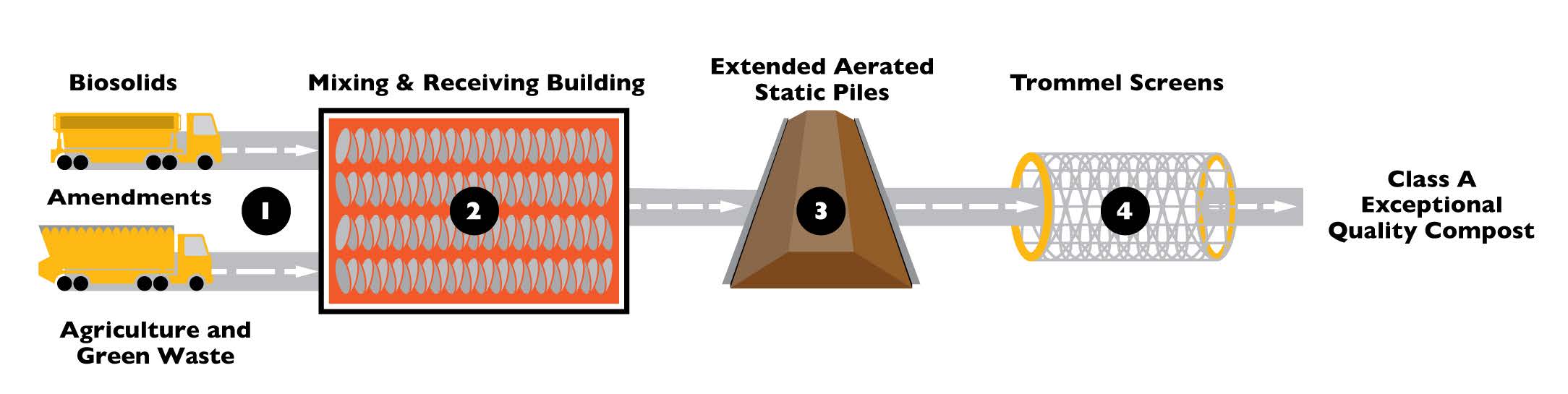 |
|
The Tulare Lake Composting process protects the environment.
|
Class A Exceptional Quality Compost is available for purchasing in bulk quantities from Tulare Lake Compost. Increases soil fertility and crop yield, provides for a slow release of nitrogen, improves water retention capacity, improves plant resistance to diseases, provides Nitrogen, Phosphorus, and Potassium (NPK), and provides micronutrients and trace elements.
|
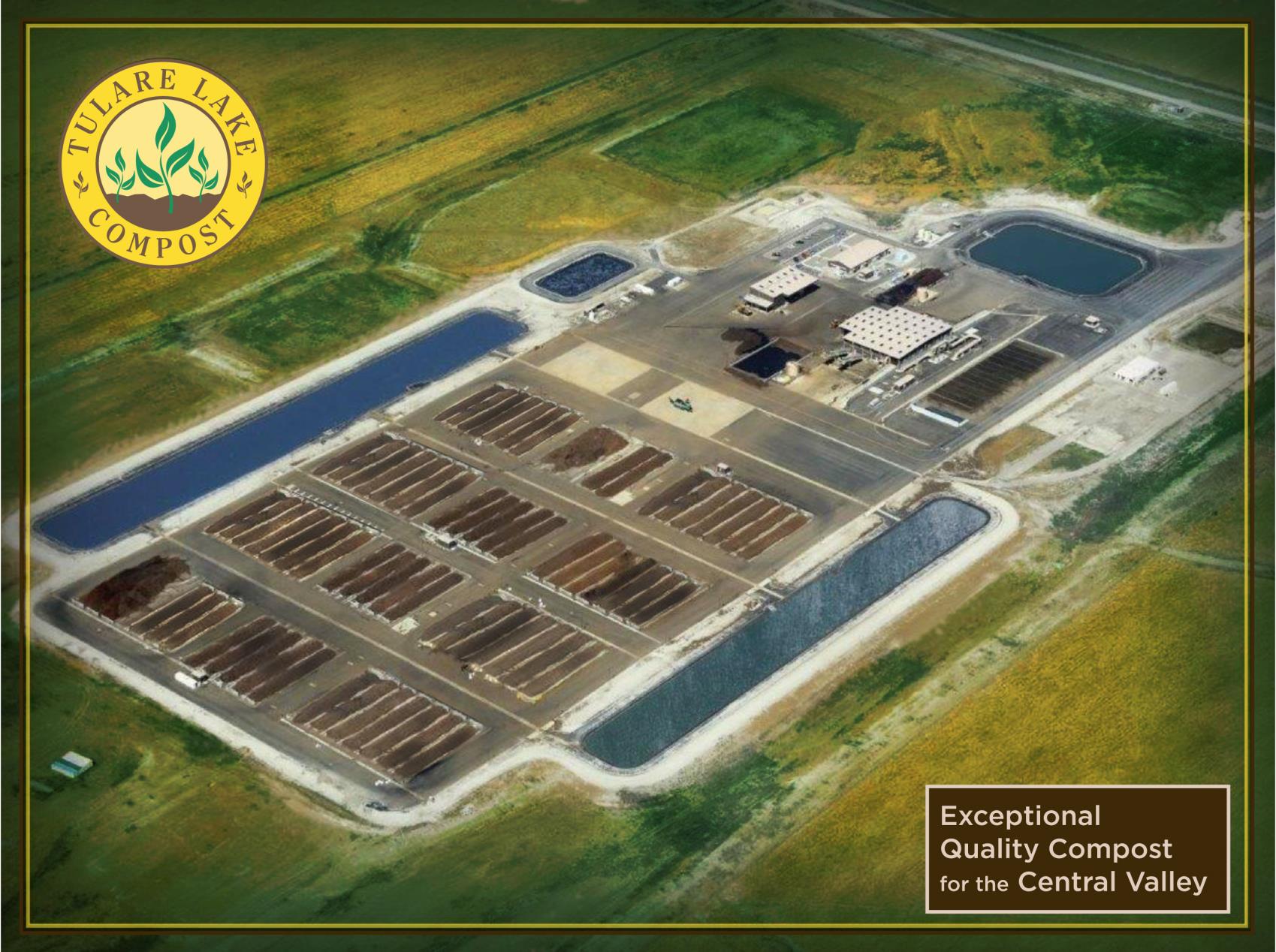
|
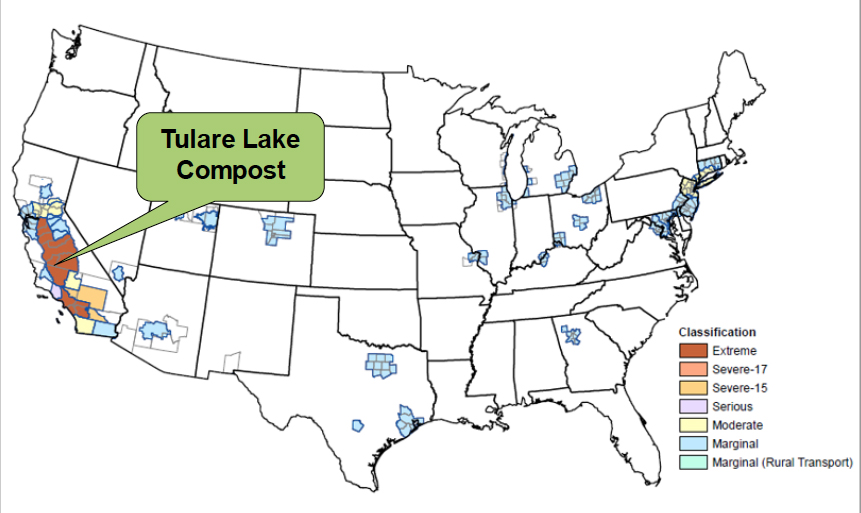
|
Tulare Lake Compost began operation in 2016. "Campus" including mixing building, scales, admin, and maintenance sized for up to 300,000 wet tons per year. Compost area would have to be expanded to accomodate extra capacity. Expansion of next two phases would occur to the east. Phase 4 and 5 would be built with new campus to the south.
|
This map shows the regions in the nation which are not meeting the standards for ozone, and there are only two regions which are in extreme nonattainment, and they are both located in California which are the South Coast Air Basin and San Joaquin Valley. And Tulare Lake Compost is located right in the middle of one of them. What this means is the local air district must closely regulate emissions to reduce pollutant levels.
|
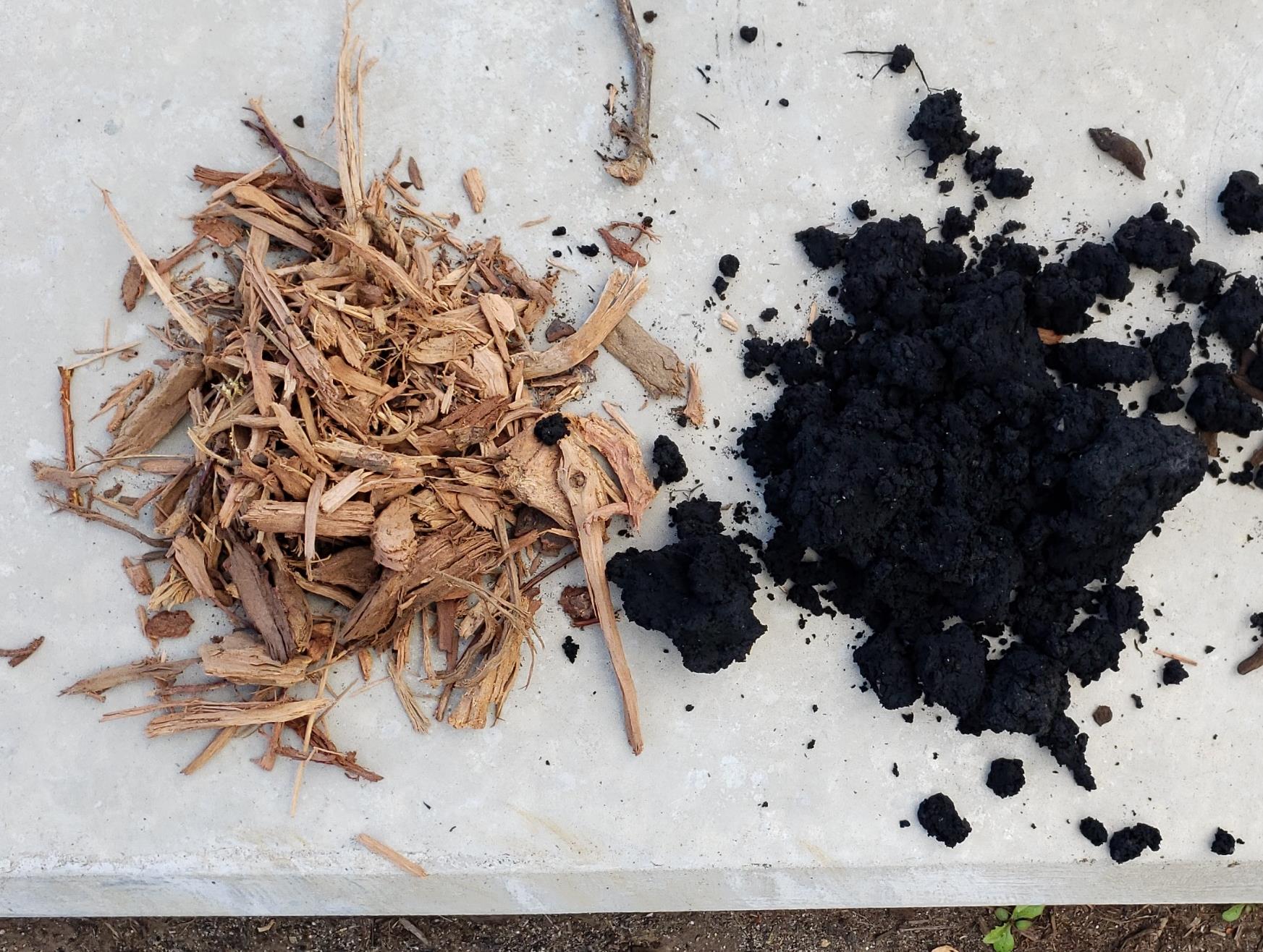
|
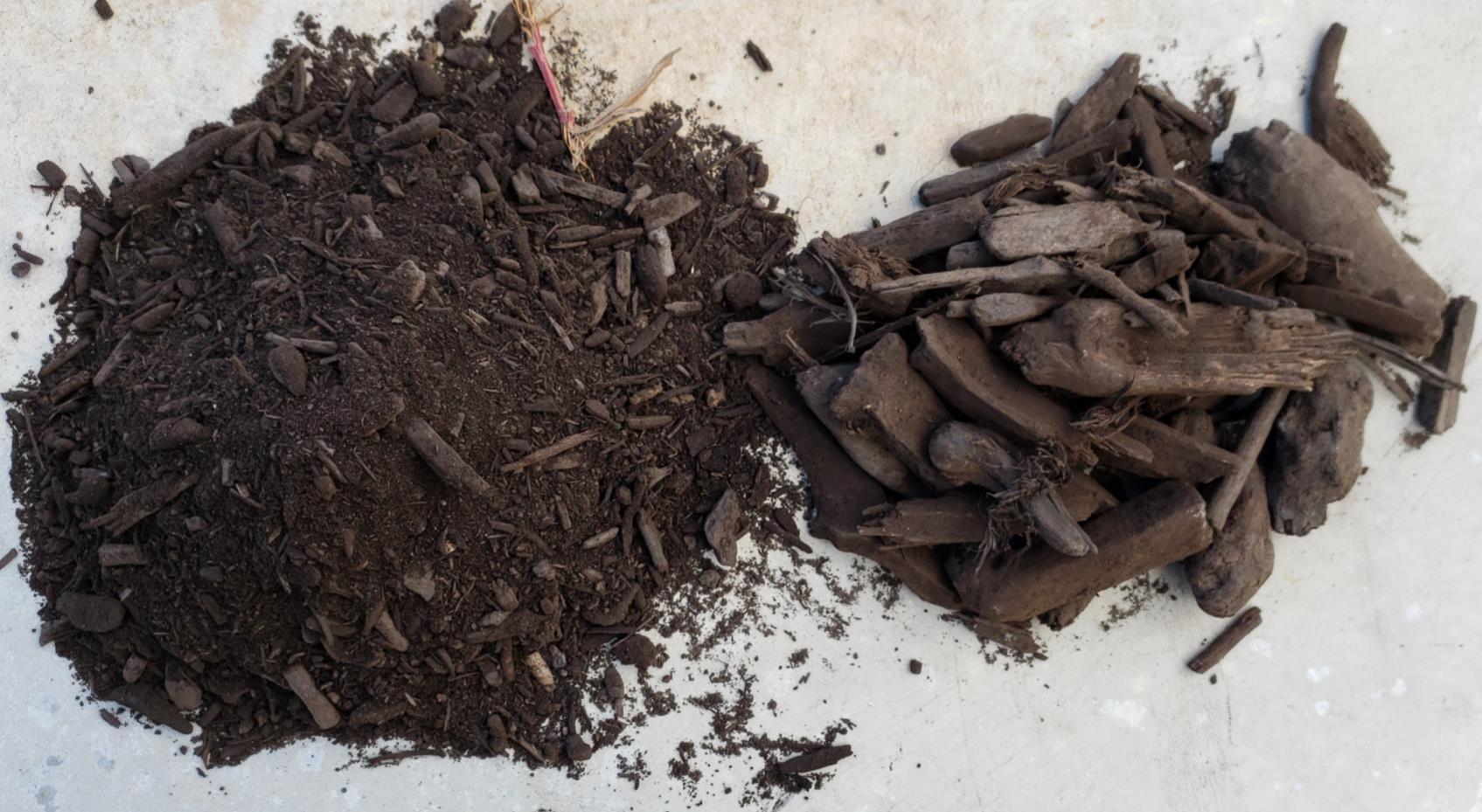
|
Agricultural Wood Waste diverted from uncontrolled burning operations, Biosolids diverted from landfill operations.
|
Nutrient rich compost, Screened Agricultural Wood Waste, recycled b ack into the composting process.
|
|
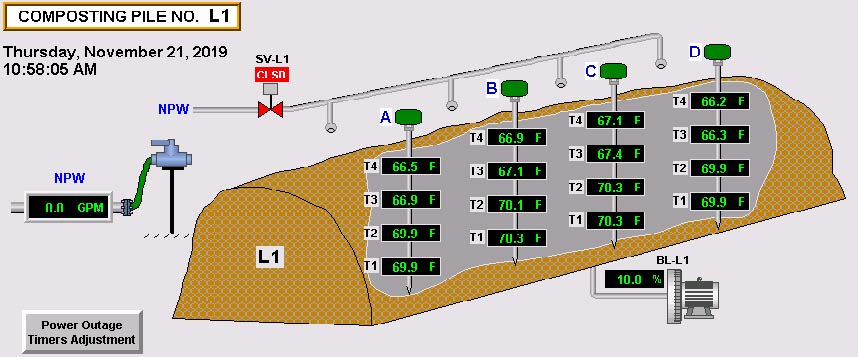
|
Clean screening operations separated finished nutrient rich compost from screen wood waste that is recycled back into the composting process.
|
TLC's SCADA (Supervisory Control And Data Acquisition) System improves our data monitoring capabilities and standardizes the collection and trending of operational parameters. SCADA integration has greatly improved our ability to monitor operations, even remotely, and respond in a timely manner. This screenshot from the SCADA system shows the individual probes with temperature sensors at multiple depths, the irrication control valve, and the blower speed control.
|
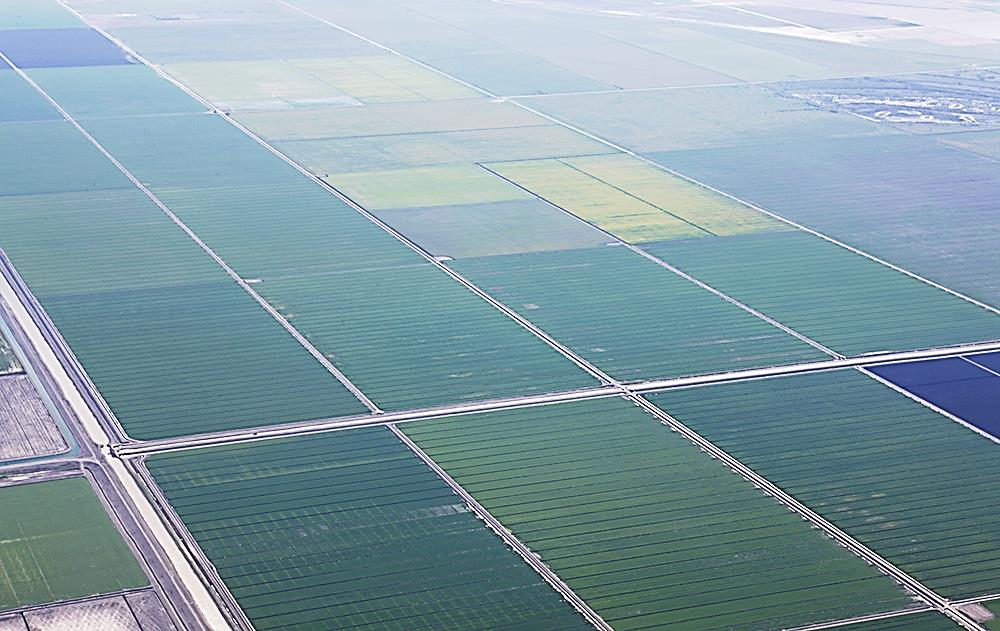
|
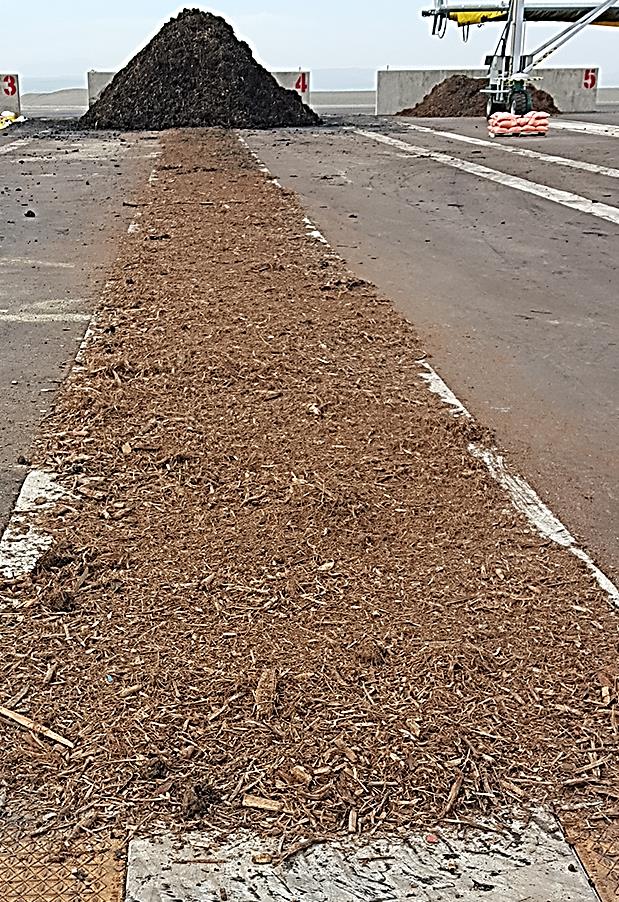
|
Productive Tulare Lake Compost neighboring farmland receives nutrient rich compost, which enhancing water and soil conservation and improves crop yields.
|
Agricultural wood waste diverted from open burning is used to improve process oxygen content through use as base when building ASPs (aerated static piles).
|
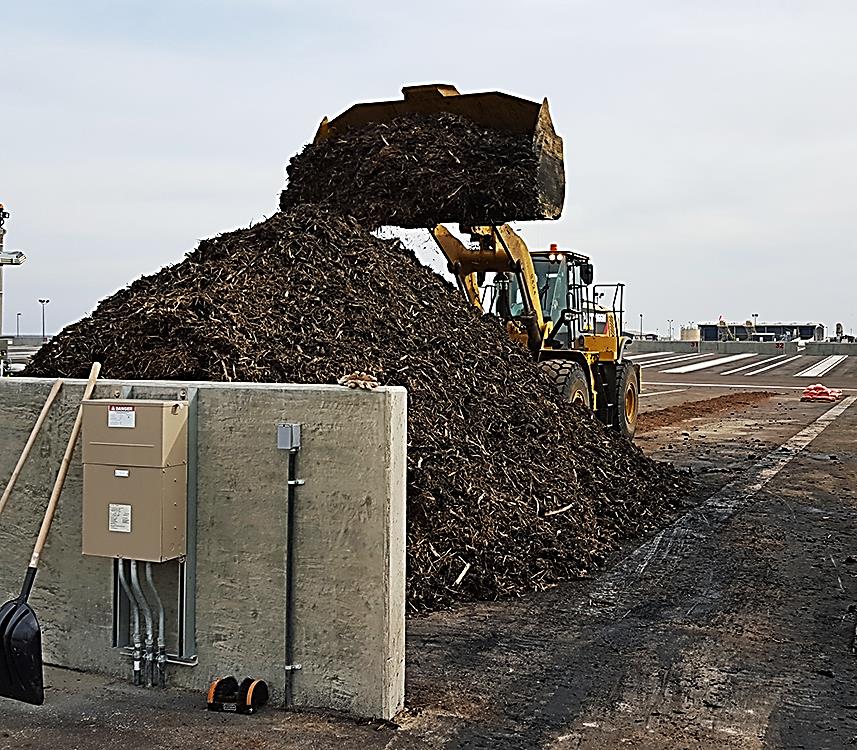
|
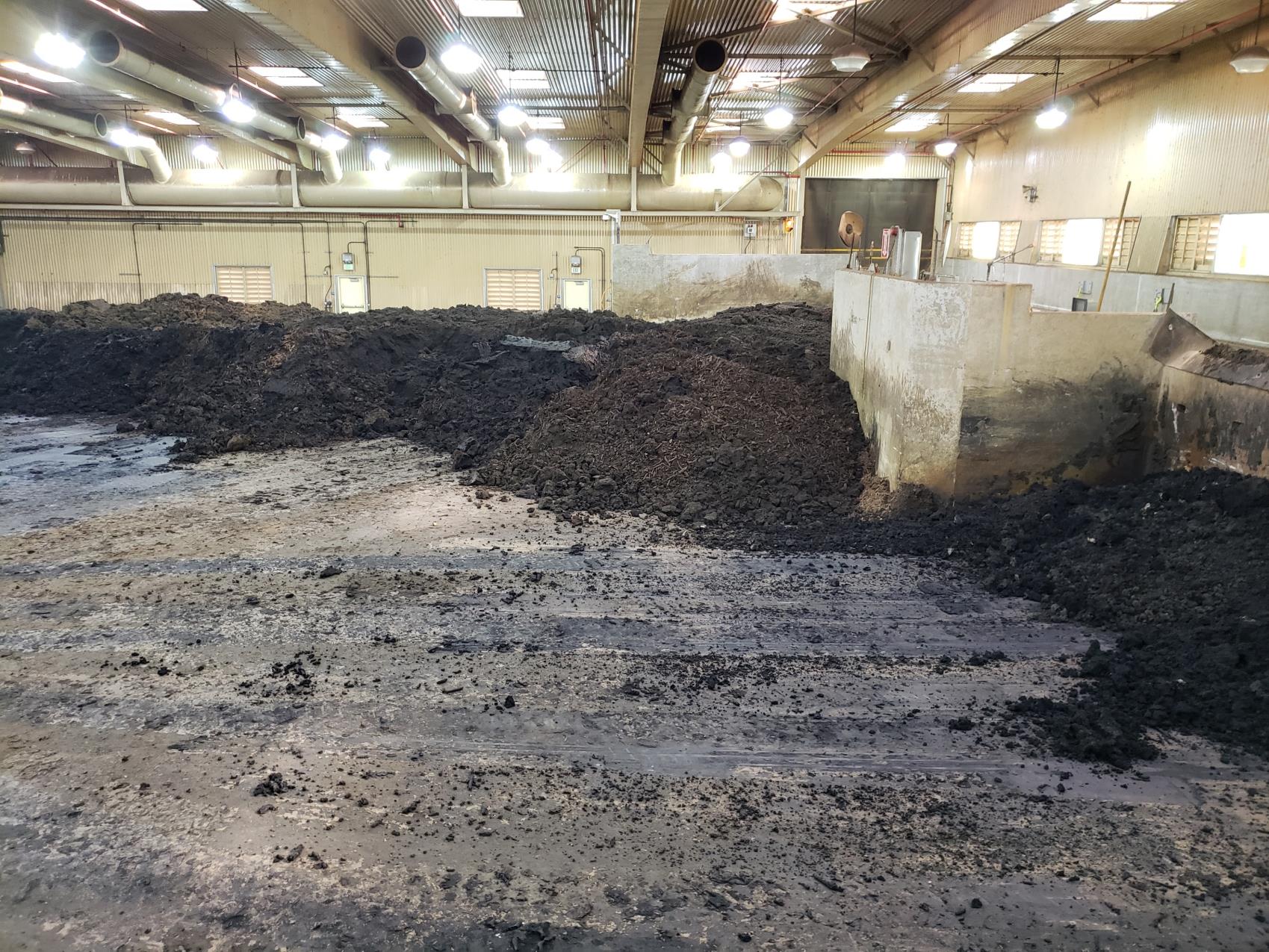
|
Tulare Lake Compost operations staff uses best management practices to keep site clean while building ASPs (aerated static piles).
|
Mixing building protects regional air quality by enclosing biosolids and wood waste mixing operations. The mixing building also includes green building features such as skylights to reduce energy consumption.
|
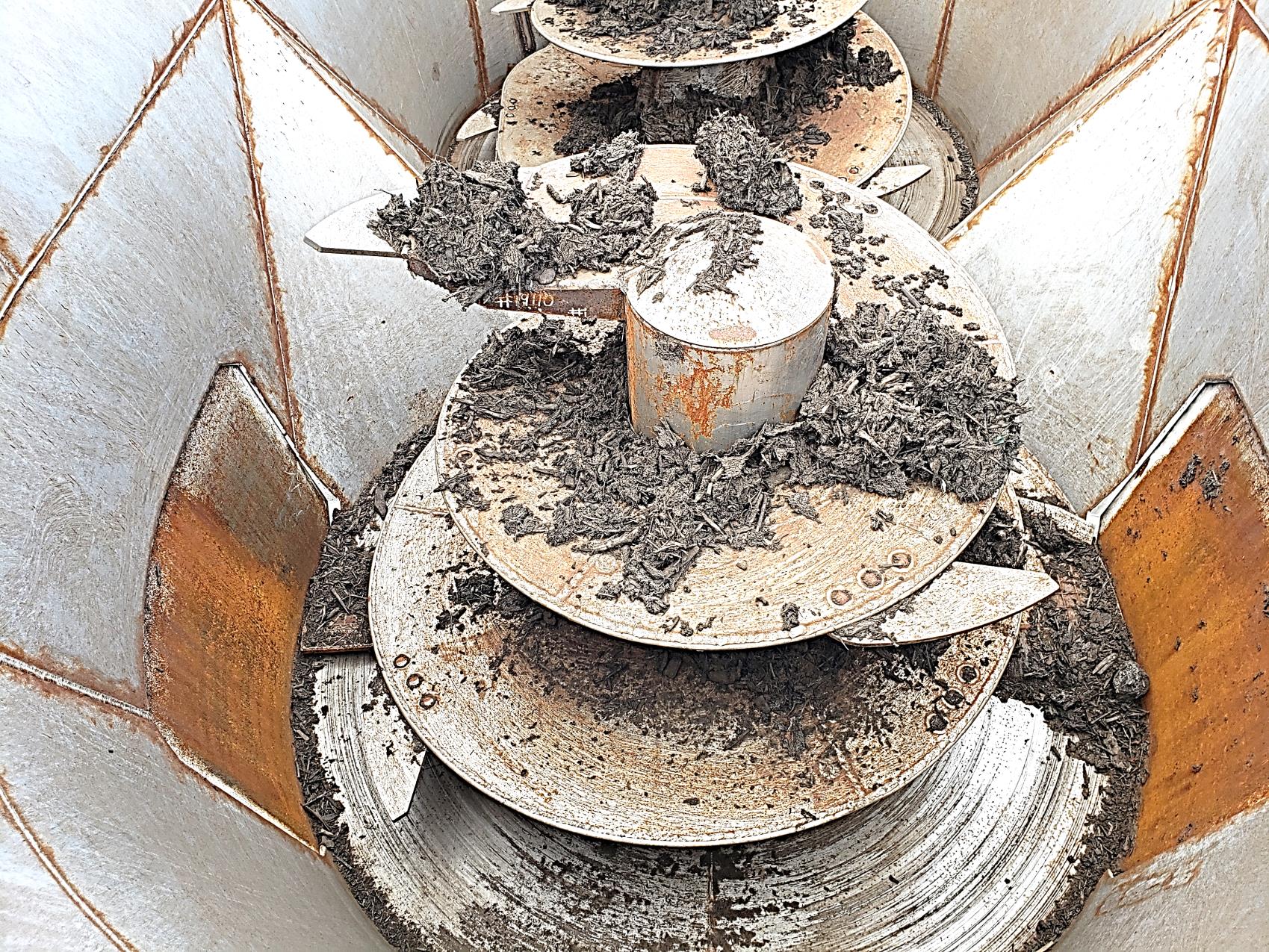
|
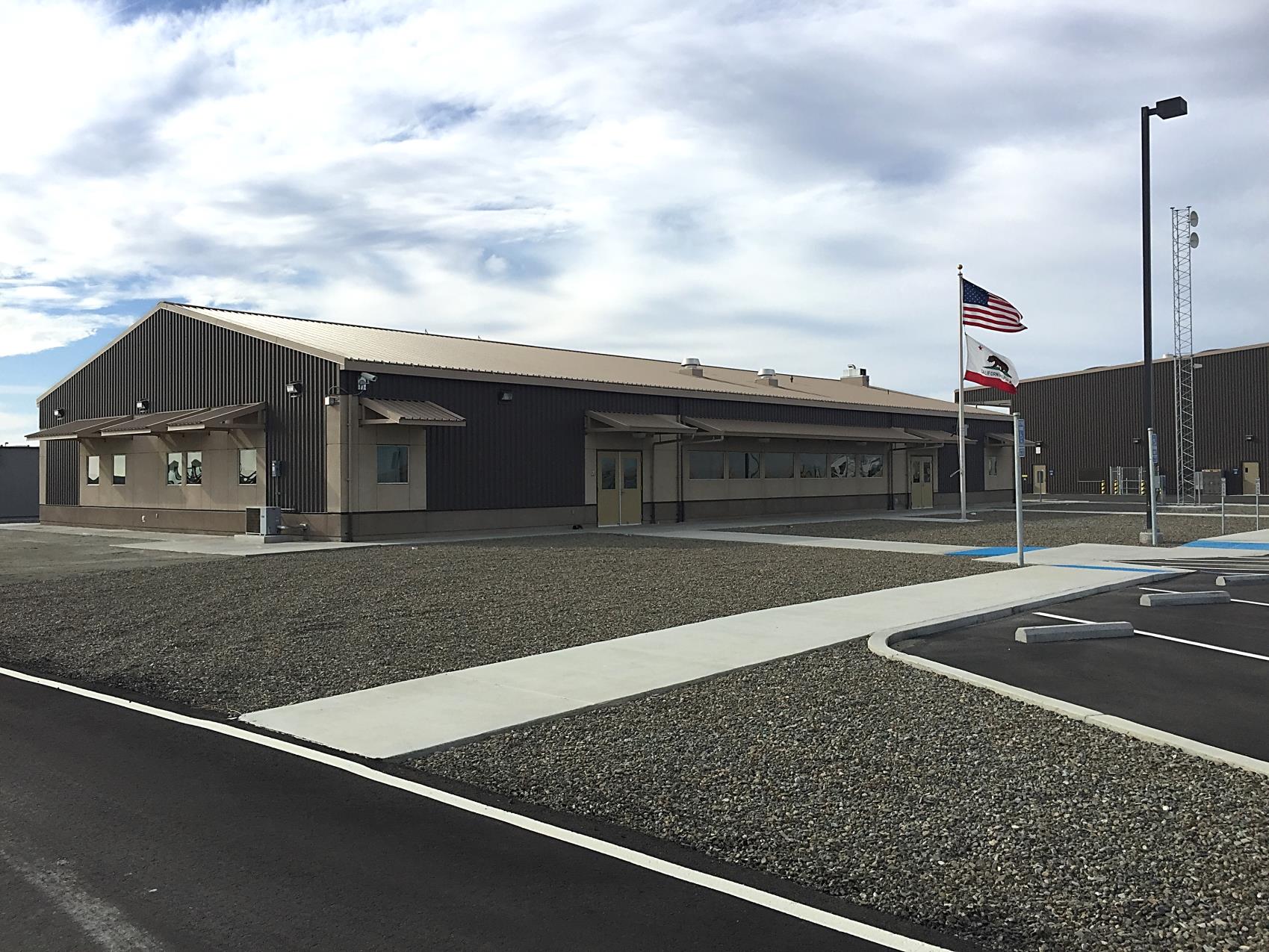
|
Mixer (interior view).
|
TLC's Administrative Office Building is LEED (Leadership in Energy and Environmental Design) Certified.
|
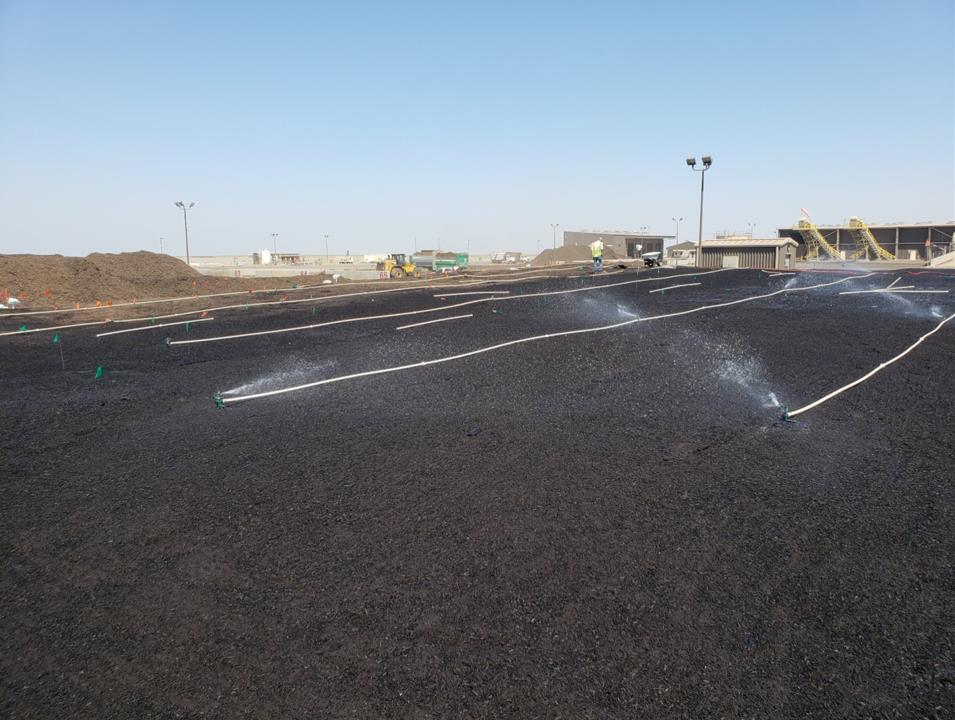
|
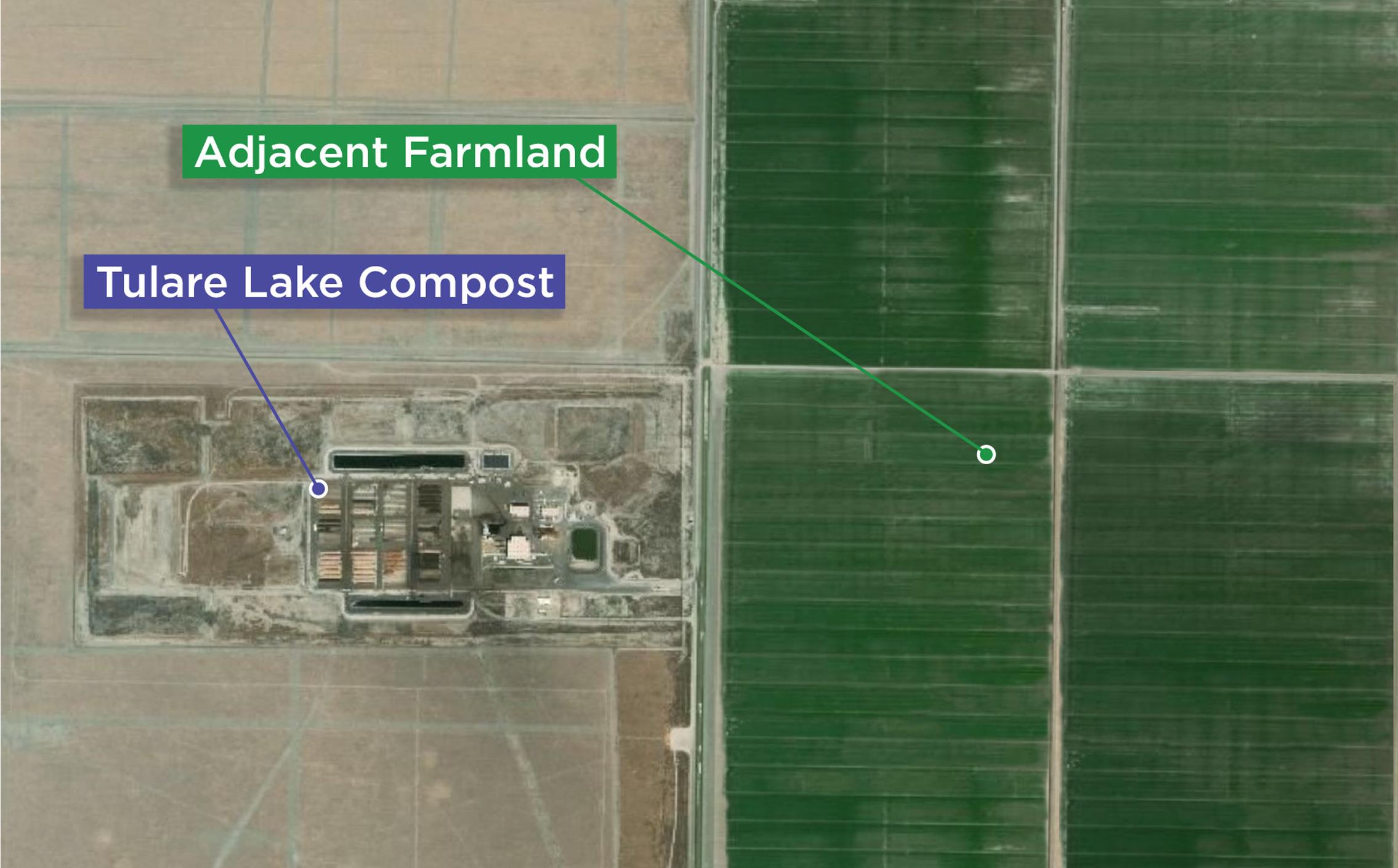
|
The process logic controller (PLC) also controlled a zoned irrigation system to control cap temperatures which insures low emissions. Irrigation was upgraded to cloud-based server controlled by mobile phone to facilitate remote and afterhours control of the irrigation system.
|
The Sanitation Districts have purchased approximately 14,500 acres of the agricultural land shown here in this slide. The proposed compost facility will encompass 175 acres of land.
|
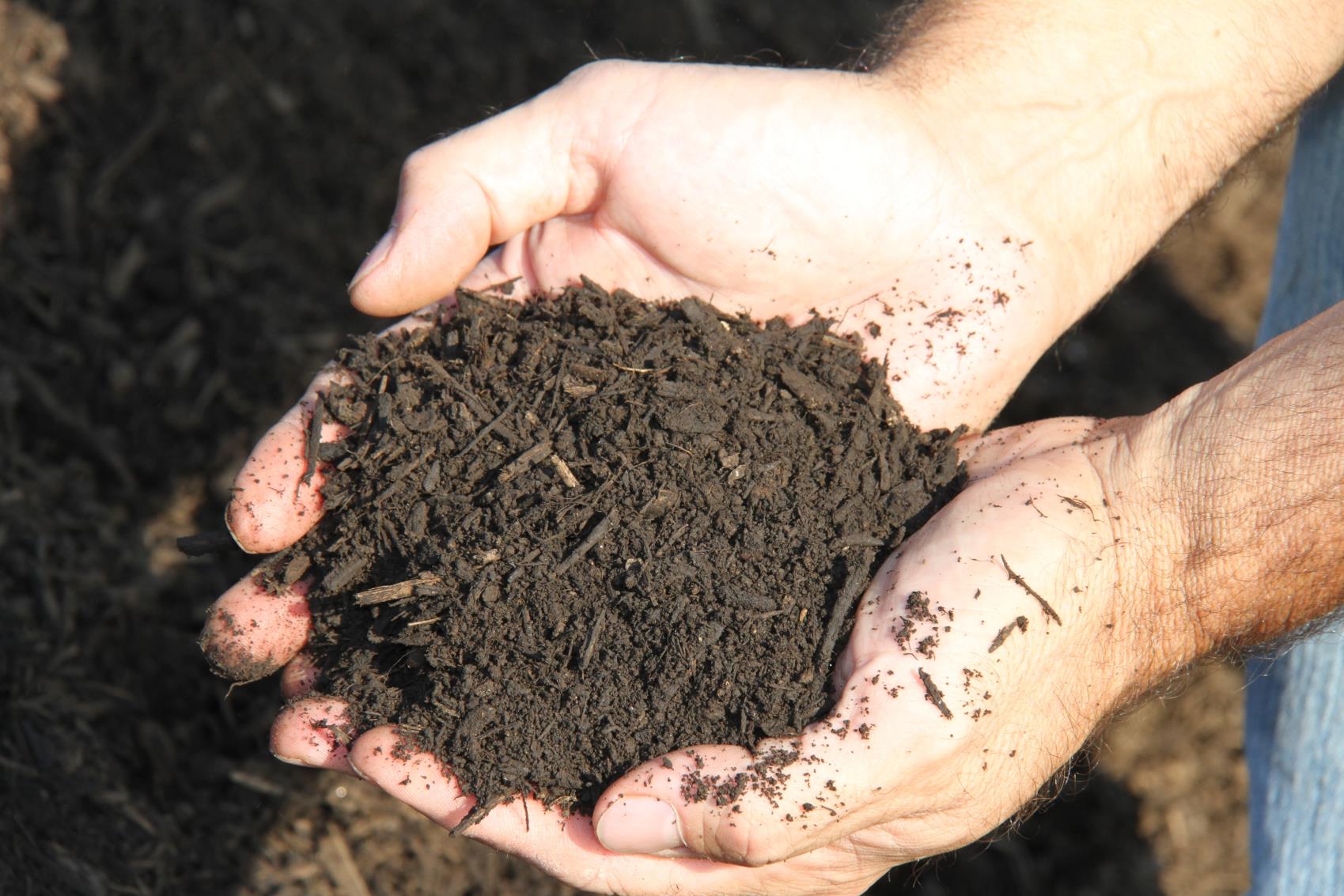
|
|
Finished nutrient rich compost ready for land application on Tulare Lake Compost neighboring farms to improve soil retention, water retention, and crop yields. Compost diverts regional agricultural wood cuttings (citrus and nuts) from open field burning helping the region achieve air quality goals.
|
|
|