2022 Excellence in Environmental Engineering and Science® Awards Competition Winner
Honor Award - Design
Michelson Water Recycling Plant Biosolids and Energy Recovery Facilities
Entrant: Black & Veatch Engineer in Charge: James H. Clark, P.E., BCEE Location: Irvine, California Media Contact: Bruce Moores
Entrant Profile
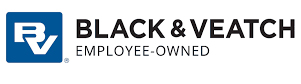
Black & Veatch (BV) provides integrated engineering, procurement, consulting, and construction services to public and private clients, promoting the resilience and reliability of infrastructure assets that improve the quality of life.
The company has nearly 100 years of experience in biosolids processing and management. It designed the Biosolids and Energy Recovery Facility to process all biosolids produced at the Irvine Ranch Water District’s Michelson Water Recycling Plant, use the energy and heat generated during solids processing, and deliver a final product for beneficial use as fertilizer or e-fuel.
Project Description
Overview
The Irvine Ranch Water District (IRWD) added complete biosolids handling and treatment facilities to the Michelson Water Recycling Plant (MWRP) following a project to expand the plant’s capacity to 28 million gallons per day (MGD). Previously, all biosolids from the MWRP were conveyed to a neighboring agency for processing, reuse, and disposal. IRWD decided to implement solids handling facilities at the MWRP based on economic and non-economic factors in support of its mission to “provide reliable, high-quality water and sewer service in an efficient, cost-effective manner and environmentally sensitive way that provides a high level of customer satisfaction.”
Integrated Approach
The new facilities were designed to process all biosolids produced at the MWRP, capture and reuse the energy generated during processing, and deliver a final product that can be used as a commercial fertilizer or fuel.
Comprehensive Technology
Sludge Thickening
Primary sludge (PS) and waste activated sludge (WAS) are transferred from the existing liquids process to the new Dewatering Facility for thickening prior to digestion. The facility includes four (4) solid-bowl centrifuges for thickening PS and WAS separately or as combined PS/WAS. Prior to thickening, the sludge is passed through strain presses to remove small inorganic material that could cause plugging in the sludge dryer.
Anaerobic Digestion
Solids from the thickening process are sent to a two-stage anaerobic digestion process. Step one is the acid phase, done in three concrete acid-phase digesters with an approximate retention time of 1.5 days. Sludge from the acid-phase digesters is pumped to the methane phase (three 1.5 million gallon egg-shaped) digesters. The two-step process provides greater stability in mesophilic anaerobic digestion by prehydrolyzing and pre-acidifying feed sludge, making it more amenable for anaerobic digestion.
Dewatering
After digestion, sludge is sent via gravity to two holding tanks that provide intermediate storage prior to the dewatering/drying processes. Dewatering is done through three solid bowl centrifuges, yielding a sludge cake of 22-25 percent dryness for feeding into the dryer.
Drying
Dewatered sludge is fed through a rotary drum thermal dryer, yielding a product with 92 percent dryness. The system includes feed pumps, and the dryer process and emission controls consist of a venturi wet scrubber followed by a regenerative thermal oxidizer. Dried product is stored in two elevated silos with gravity-feed truck loading.
Energy Recovery
Energy recovery in the form of electric power generation and heat recovery was integrated in the design.
Gas Treatment
Digester gas goes through a two-step cleaning process to remove hydrogen sulfide and siloxanes prior to use in the dryer, boiler, or microturbines.
Microturbines
Energy recovery is achieved through five 200-kw microturbines. Treated digester gas is directed to the microturbines for energy production as well as heat production for digester heating. A BTU content monitor is used to monitor BTU content of the gas, with a natural gas blending station to maintain optimum BTU feed to the microturbines.
FOG Receiving
The facility includes a Fats, Oils, and Grease (FOG) receiving station. Trucked-in FOG is screened, heated, and metered into the digestion process slowly to enhance digester gas production, allowing for greater energy recovery.
Centrate Treatment
Centrate from the digested sludge dewatering is high in ammonia. To limit impacts on the liquid treatment process, an ammonia-removal process was included. The process consists of two sequencing batch reactors (SBR) that use fine-bubble aeration to biologically remove ammonia from the centrate and allow for settling of solids carryover, which are subsequently collected and returned to the sludge thickening process for treatment.
Quality
The final biosolids product meets the Class A requirements for Part 503 of the U.S. Environmental Protection Agency (EPA) Title 40 of the Code of Federal Regulations (CFR).
Originality/Innovation
The design provided a fully integrated biosolids treatment system using state-of-the art equipment for thickening, digestion, dewatering, and thermal drying of biosolids while incorporating energy production and waste-heat capture to offset energy consumption. Inclusion of a two-step acid/mesophilic digestion process for increased efficiency further enhances the effectiveness of the biosolids treatment processes.
Complexity
Challenges
The new solids treatment facilities were designed to fit in a 6.3-acre corner of the existing treatment plant, requiring careful coordination of the processes to maximize space utilization.
Meanwhile, this area of the plant provided additional challenges, as follows.
Soil Conditions
Soil conditions, weight of the structures, and project seismic requirements required that all facilities be supported on piles. The use of concrete-driven piles was chosen and, ultimately, more than 3,000 piles were driven to support the biosolids structures.
Laydown Area
The site for the solids facilities is compact. This required, as the facilities were being constructed, careful coordination for crane, equipment, and materials staging. Remote staging areas were also used.
Impacts to Operations
During start-up of the facility, the impacts of the return flows to the existing liquids processing facilities required coordination from the operations group to get the new facilities integrated into the overall operation of the treatment plant.
Contribution to Social, Public, Environment, Economic Advancement
In addition to the main treatment of the solids, the project added ancillary processes to meet IRWD’s goals of providing a facility that is environmentally responsible and uses the available energy from the treatment process.
- Buildings were designed with sound-attenuating measures to dampen the noise of the facility.
- Foul air from each portion of the treatment process is controlled at the source and directed to a three-stage, packed-tower chemical scrubber system, minimizing the impact to the environment and surrounding communities.
- Waste gases from the drying process are collected and processed through a regenerative thermal oxidizer that destroys volatile organic compounds.
- The biosolids facilities produce sufficient biogas for energy and waste-heat capture, offsetting energy usage at the plant.
- IRWD received a financial incentive through Southern California Edison’s Self-Generation Incentive Program (SGIP) for using microturbines to produce energy from the digester gas generated through the biosolids process.
- FOG-receiving facilities allow high-strength fats, oils, and greases to be brought to the facility for processing.
Click images to enlarge in separate window.
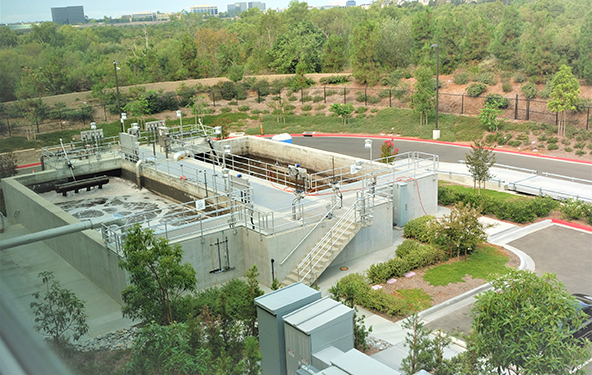 |
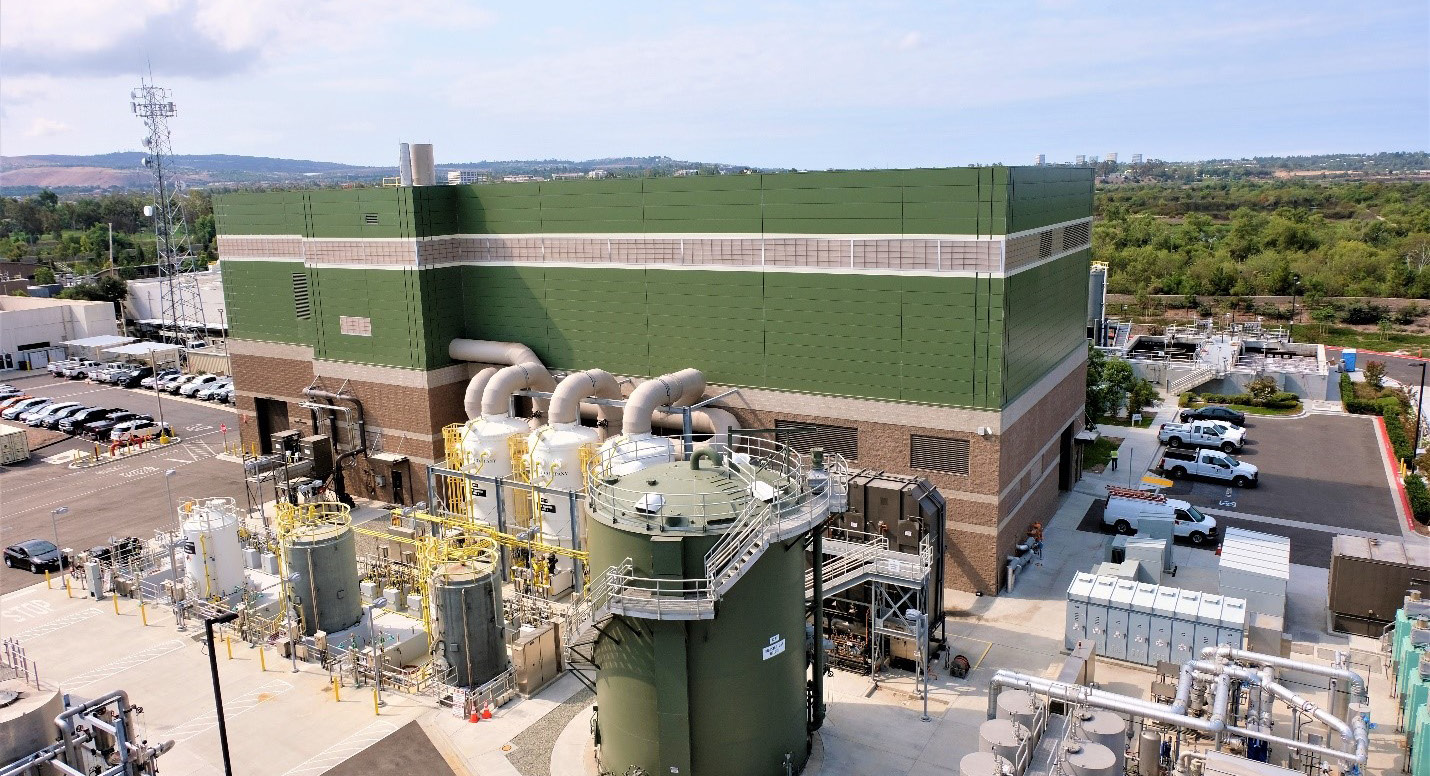 |
Aerial view of the new Biosolids and Energy Recovery Facility, showing the acid and methane phase digesters (egg-shaped) with the digester control building in the foreground and solids handling building (sludge thickening, dewatering, and drying) in the background.
|
Overview of the solids handling building with chemical storage and feed facilities to the left, digester gas storage in the center, digester gas final treatment to the right, and the solids handling building with the three-stage odor-control system in the back.
|
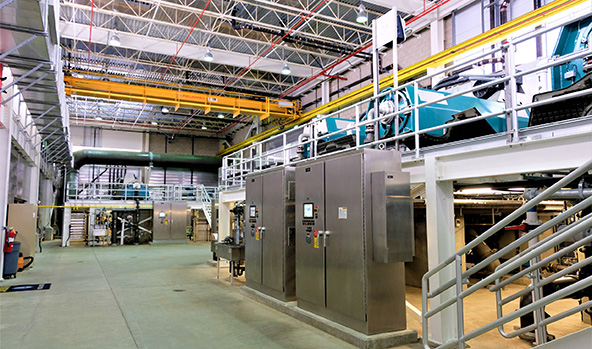 |
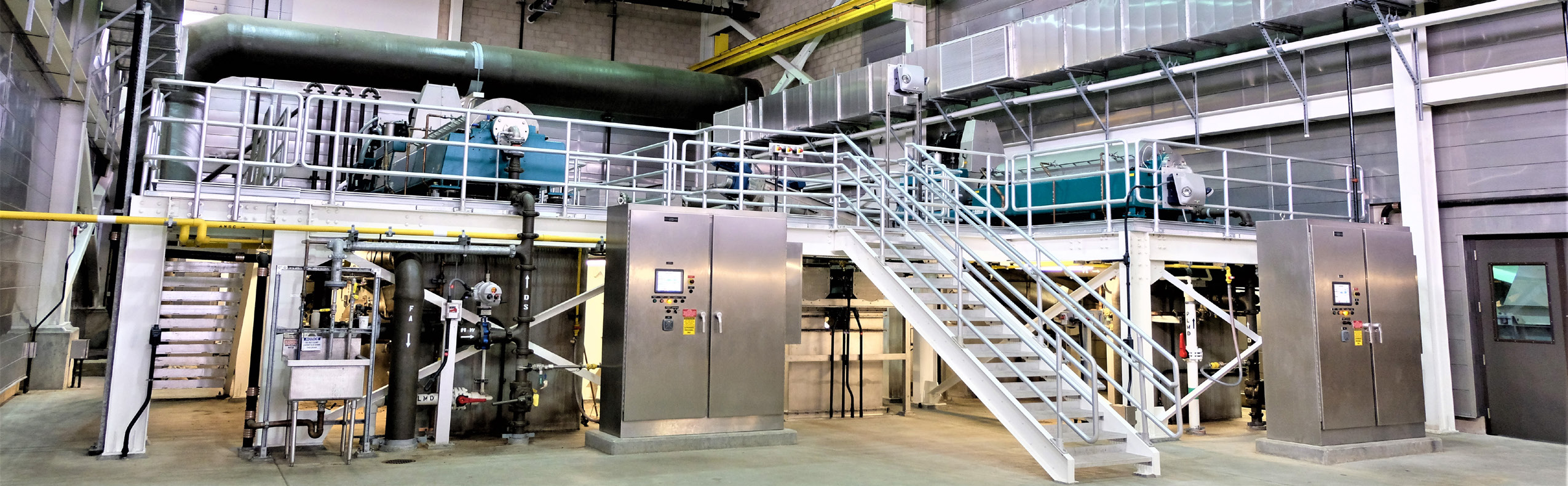 |
Centrifuges in the foreground thicken primary and waste activated sludges. Centrifuges in the background dewater digested sludge prior to drying.
|
Three centrifuges are used to dewater digested sludge. They discharge to shaftless screw conveyors, allowing the dewatered sludge cake to be directed to three feed bins below the floor, which feed to the dryer system.
|
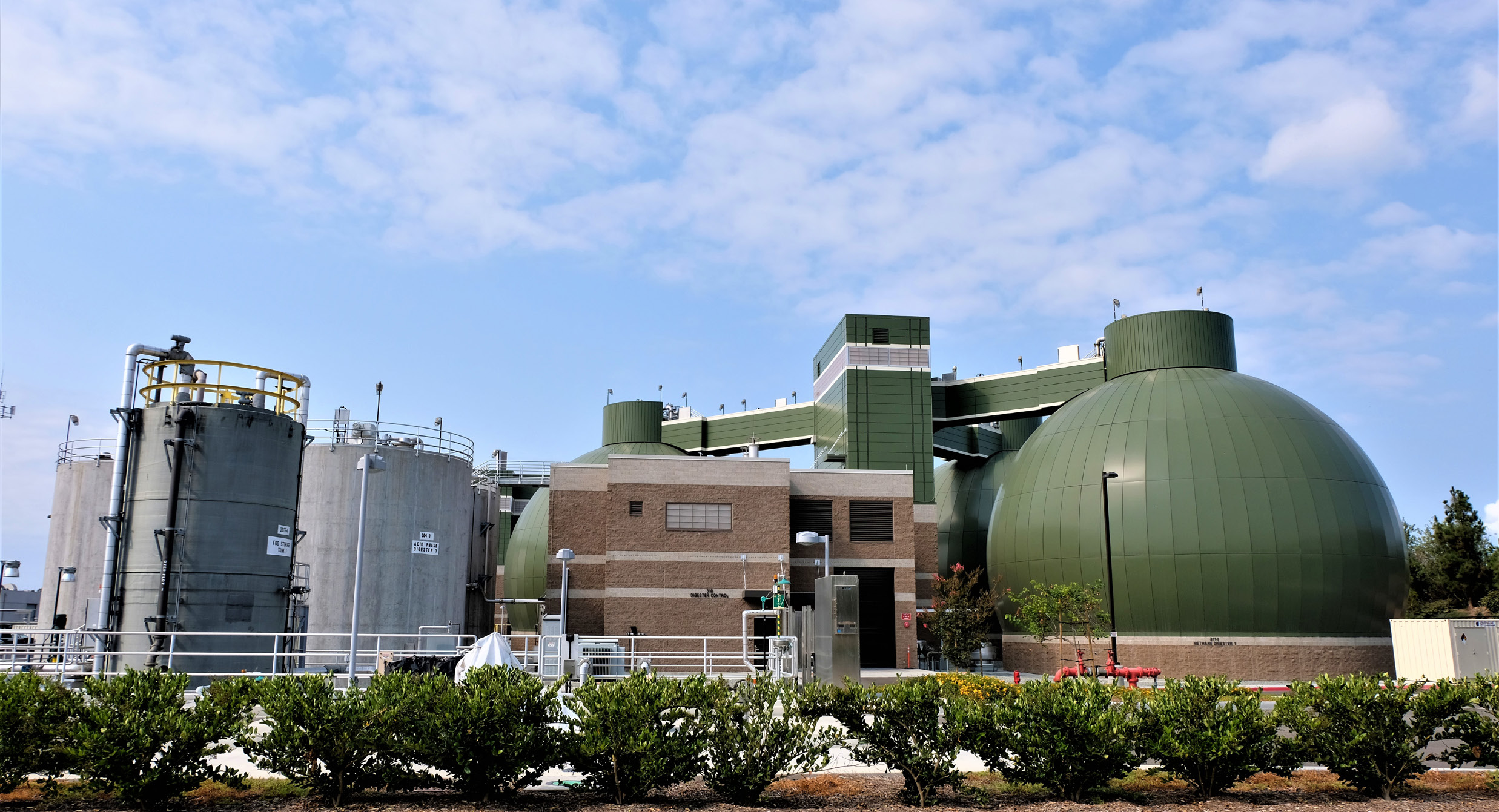 |
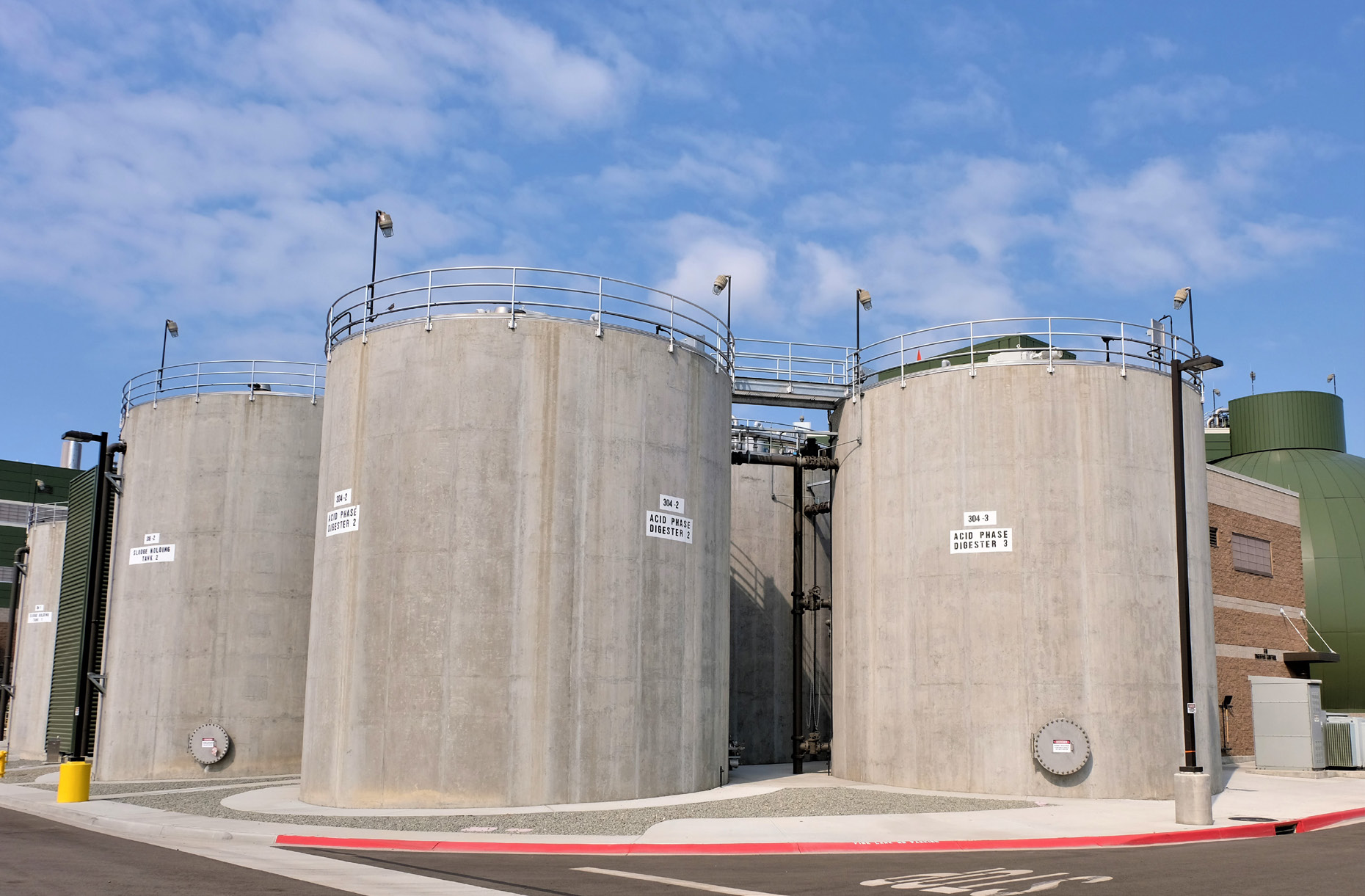 |
cid-phase digesters are shown at the left, methane-phase digesters at the right, and the digester control building in the center. The control building houses the sludge circulation, heating and other digestion process equipment. The methane-phase digesters hold 1.5 million gallons each, with an HRT of 13.5 days.
|
Acid-phase digesters: Each holds 130,000 gallons and includes a multi-blade vertical mixer plus gas collection equipment to provide a maximum hydraulic retention time of 1.5 days.
|
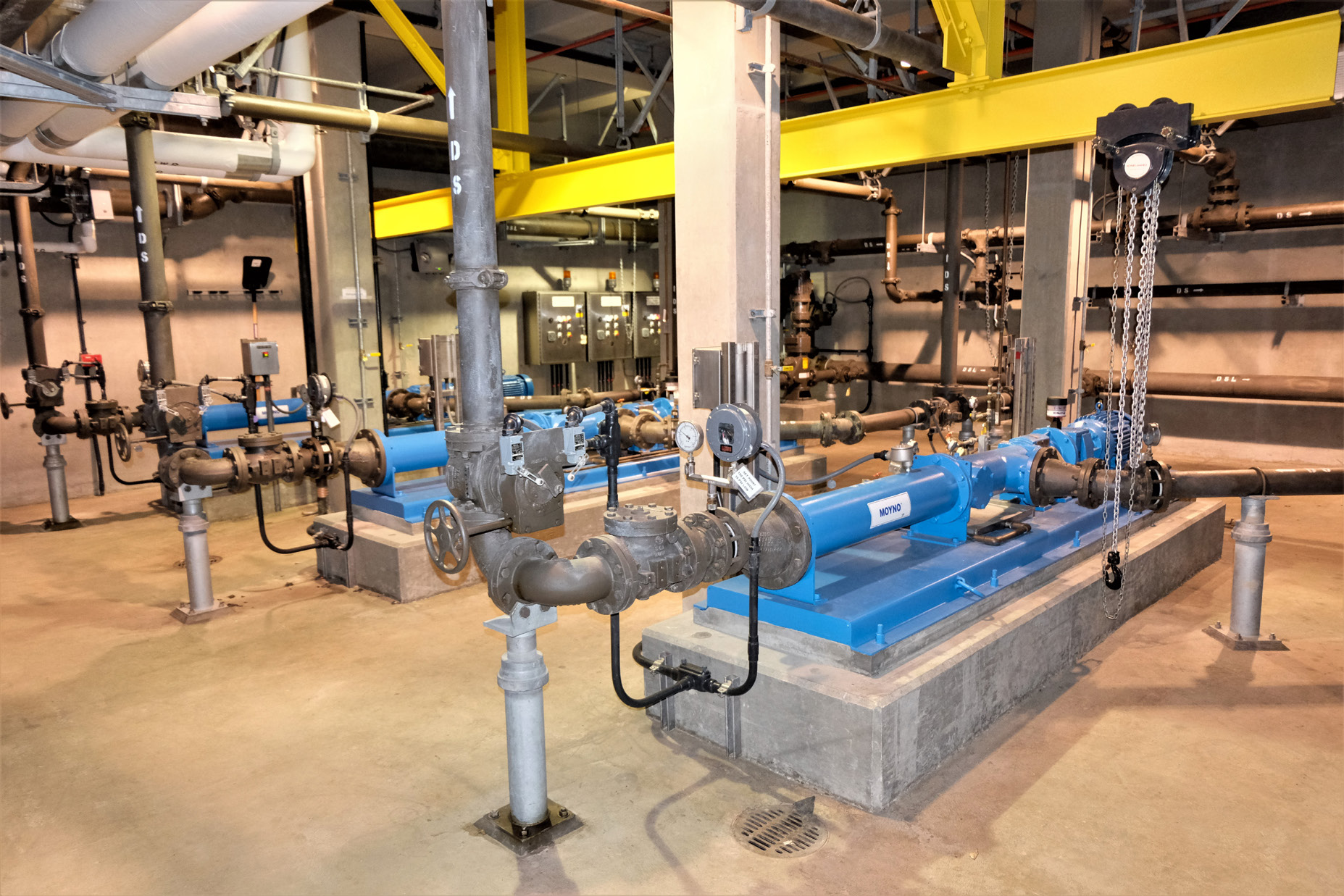
|
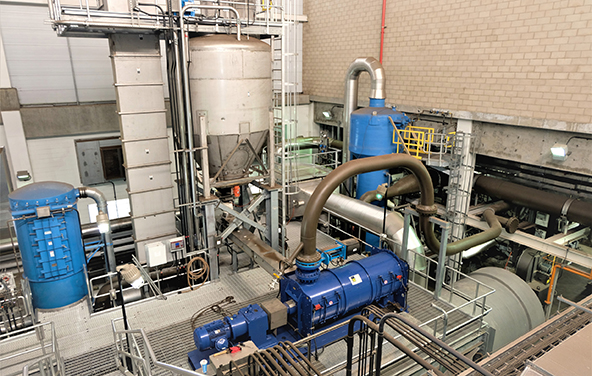 |
Dewatering feed pumps: After the digestion process, the digested sludge is directed to two holding tanks where it can be stored prior to being processed in the dewatering and drying systems. Progressing cavity pumps are used to feed the sludge to the dewatering centrifuges, each with a variable speed drive allowing for precise feed-rate control.
|
View of the sludge dryer system showing the inlet feed mixer (in dark blue). In addition, one of several dust collection and removal filters associated with the drying process is shown at the left (light blue).
|
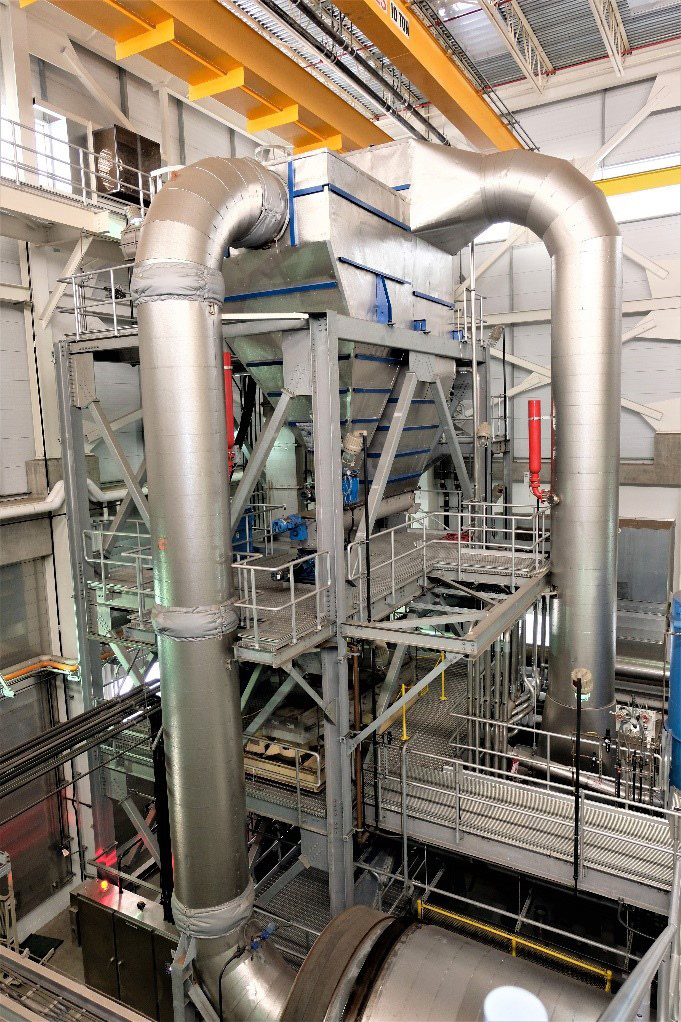 |
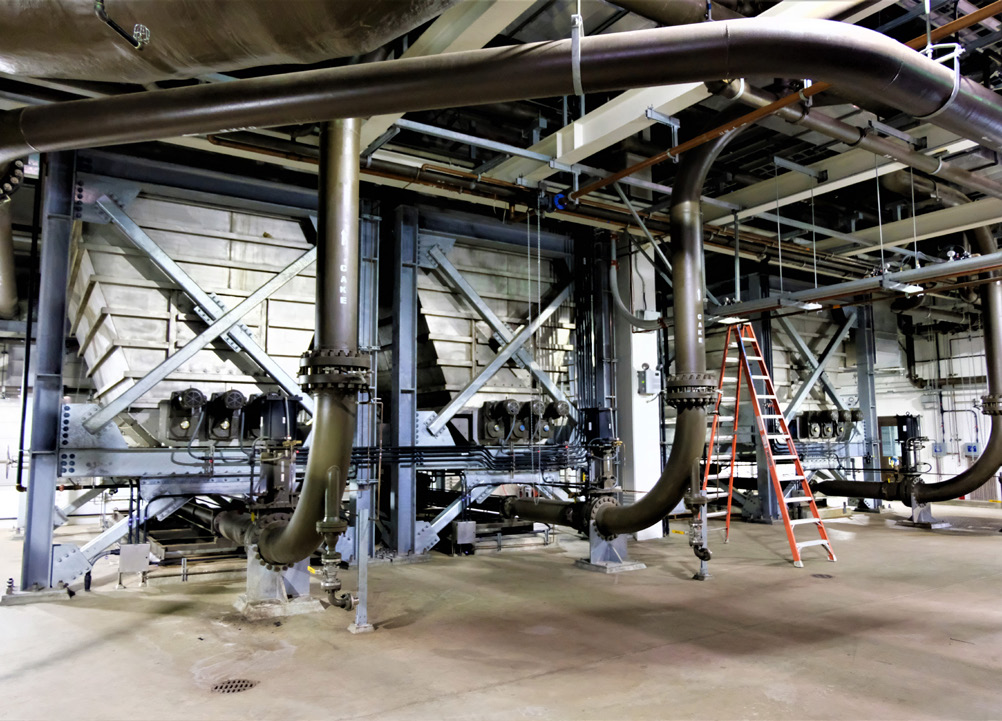 |
Side view of the sludge drying system pre-separator and elevated equipment access platform.
|
The sludge dryer system has three wet material bins and progressing cavity cake pumps to feed dewatered sludge cake to the rotary drum dryer. Each bin has a live bottom with shaftless screw conveyors that feed the cake to the pump, which feeds it to the dryer.
|
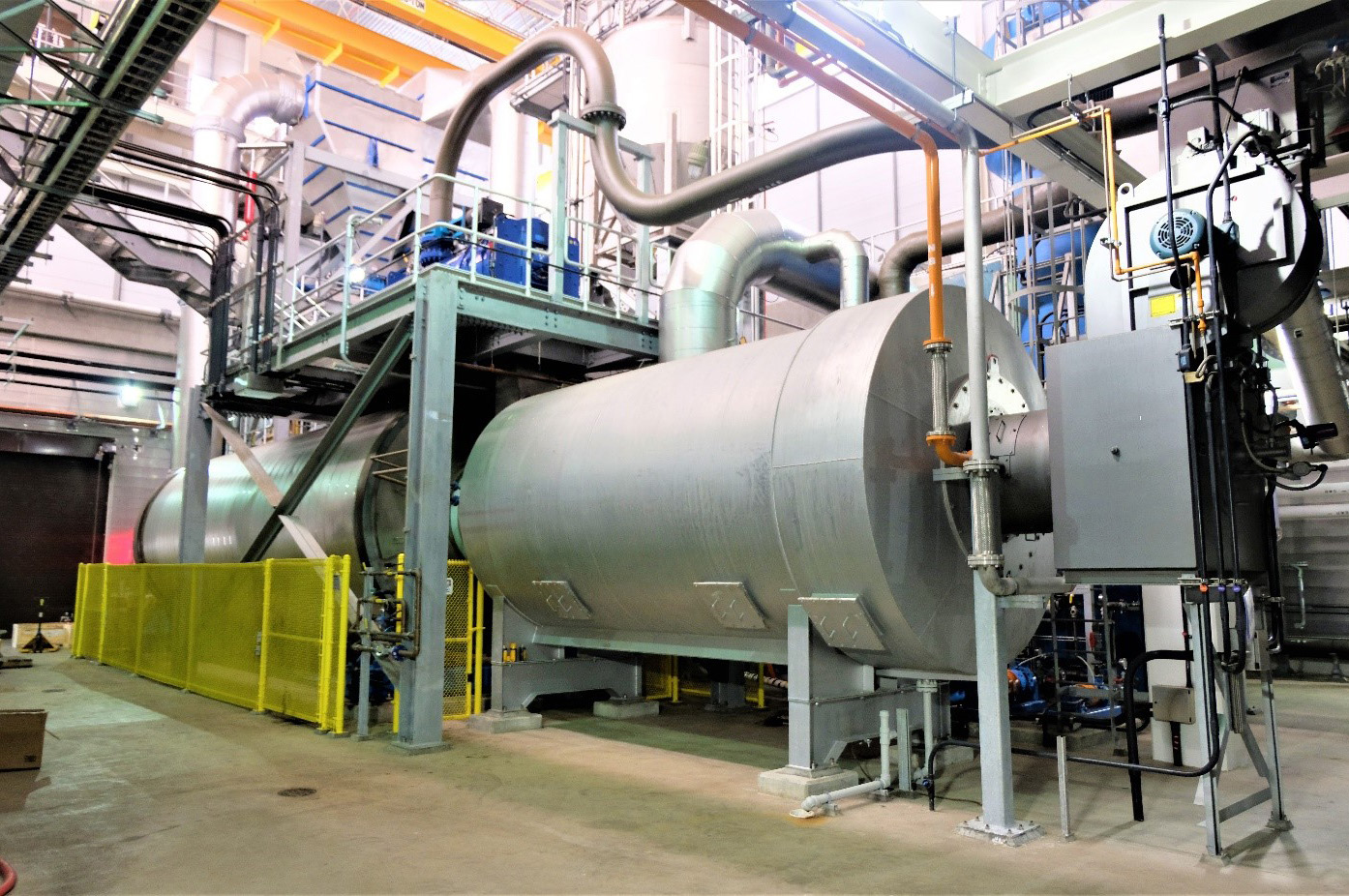
|
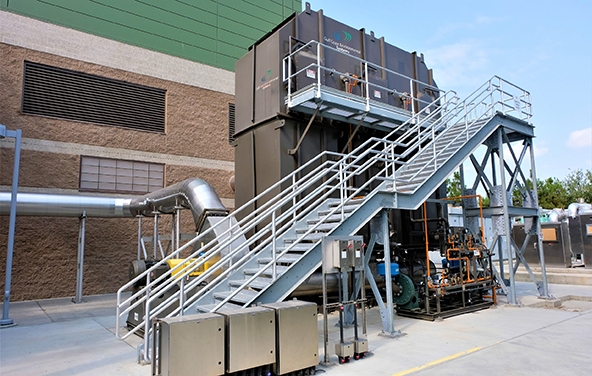 |
Sludge dryer: Dewatered digested sludge is fed to a rotary drum dryer to reduce the moisture content and produce Class A biosolids. Shown is the furnace (foreground) and the rotary drum with the wet sludge feed line above to the feed mixer.
|
A regenerative thermal oxidizer (RTO) is used as an emission-control device to treat the exhaust gases from the drying process. The RTO oxidizes volatile organic compounds (VOCs) prior to discharge to the atmosphere.
|
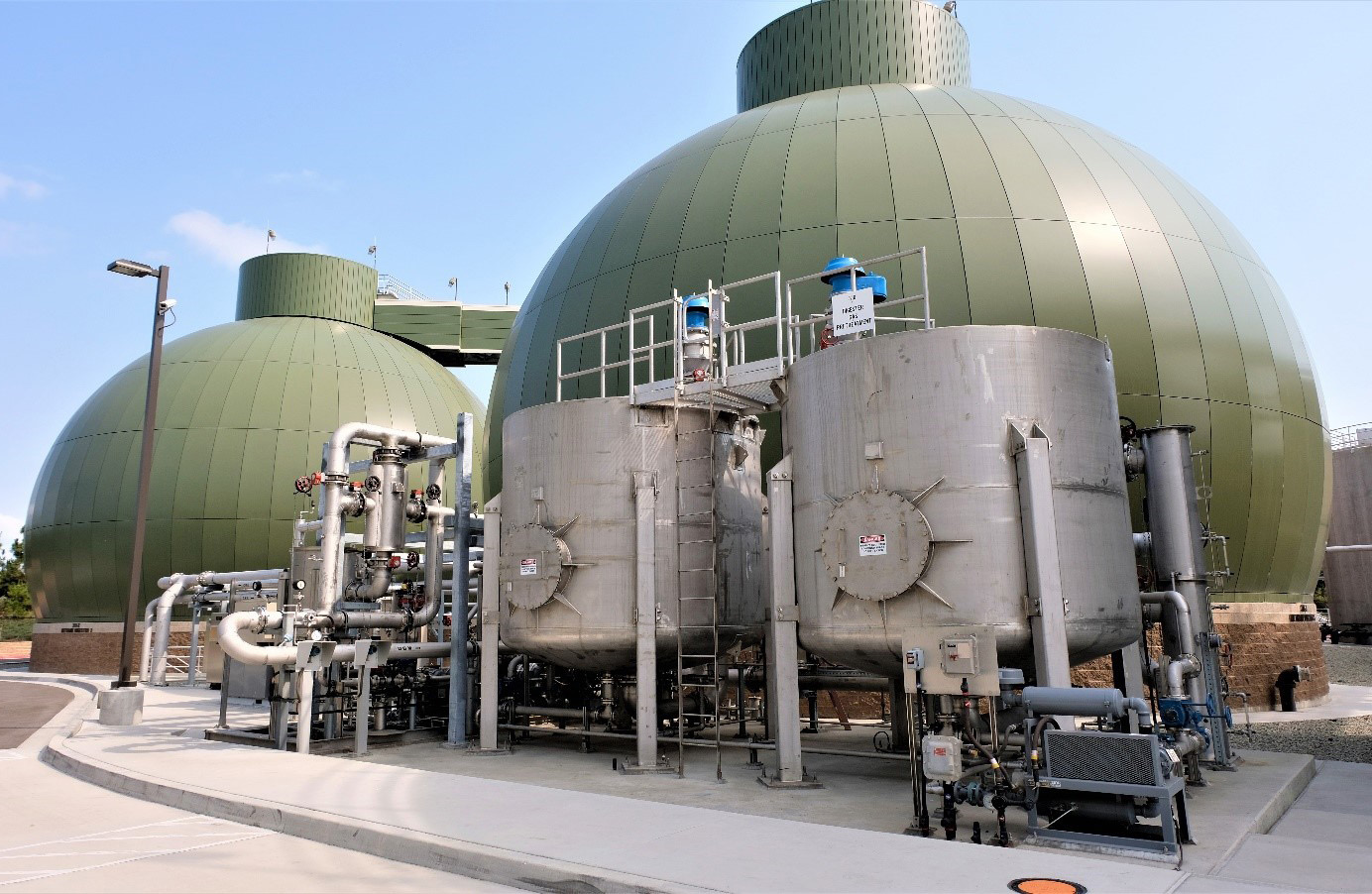 |
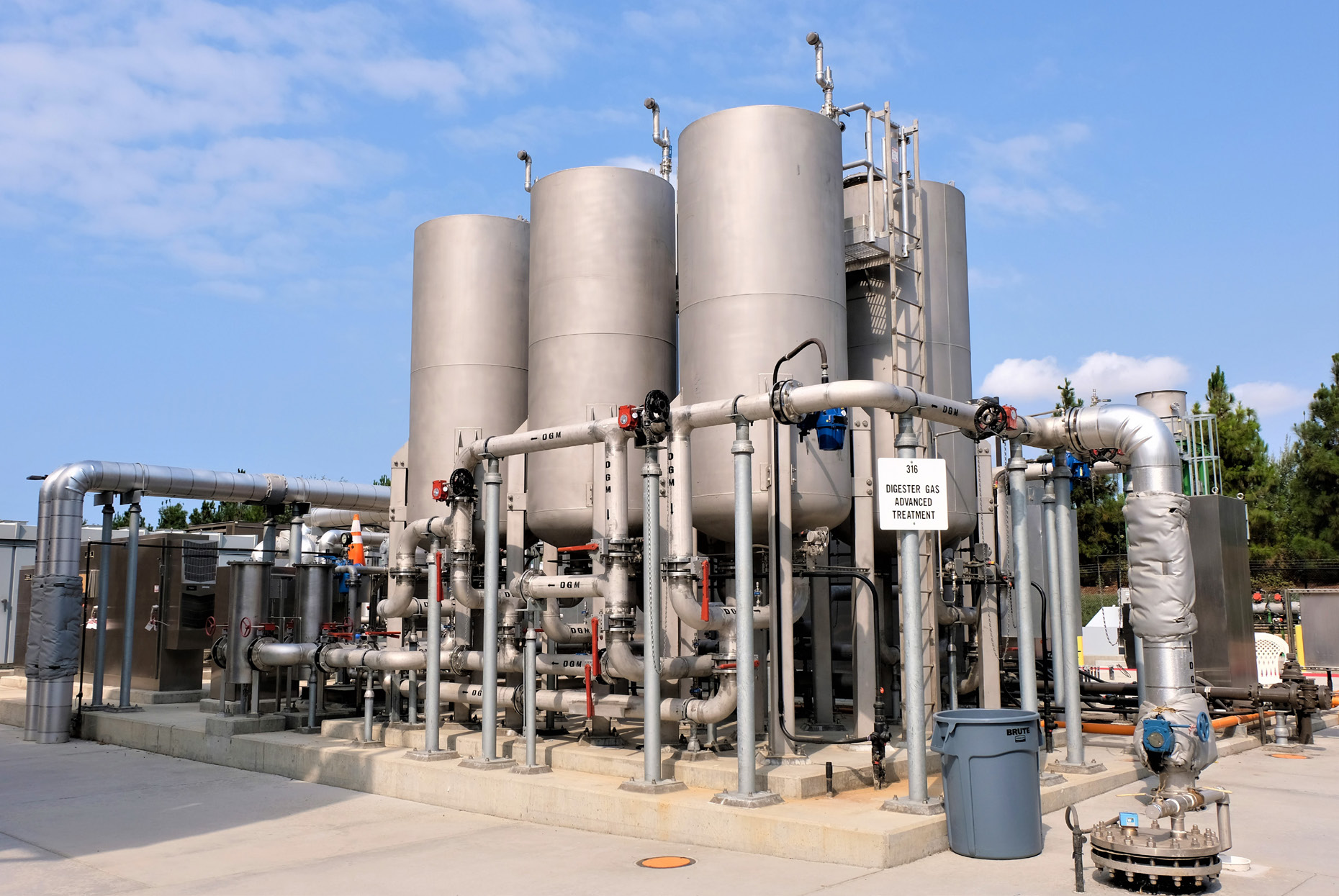 |
The digester gas pretreatment system collects the digester gas then treats it to remove hydrogen sulfide through a dual-vessel iron-sponge system with on-site regeneration capabilities. The system is upstream of all uses for the digester gas and treats 100% of the digester gas produced.
|
Downstream of the digester gas pretreatment system is the final gas treatment system. It treats all gas used in the microturbine system. This final system removes siloxanes from the digester gas that would be harmful to the microturbines.
|
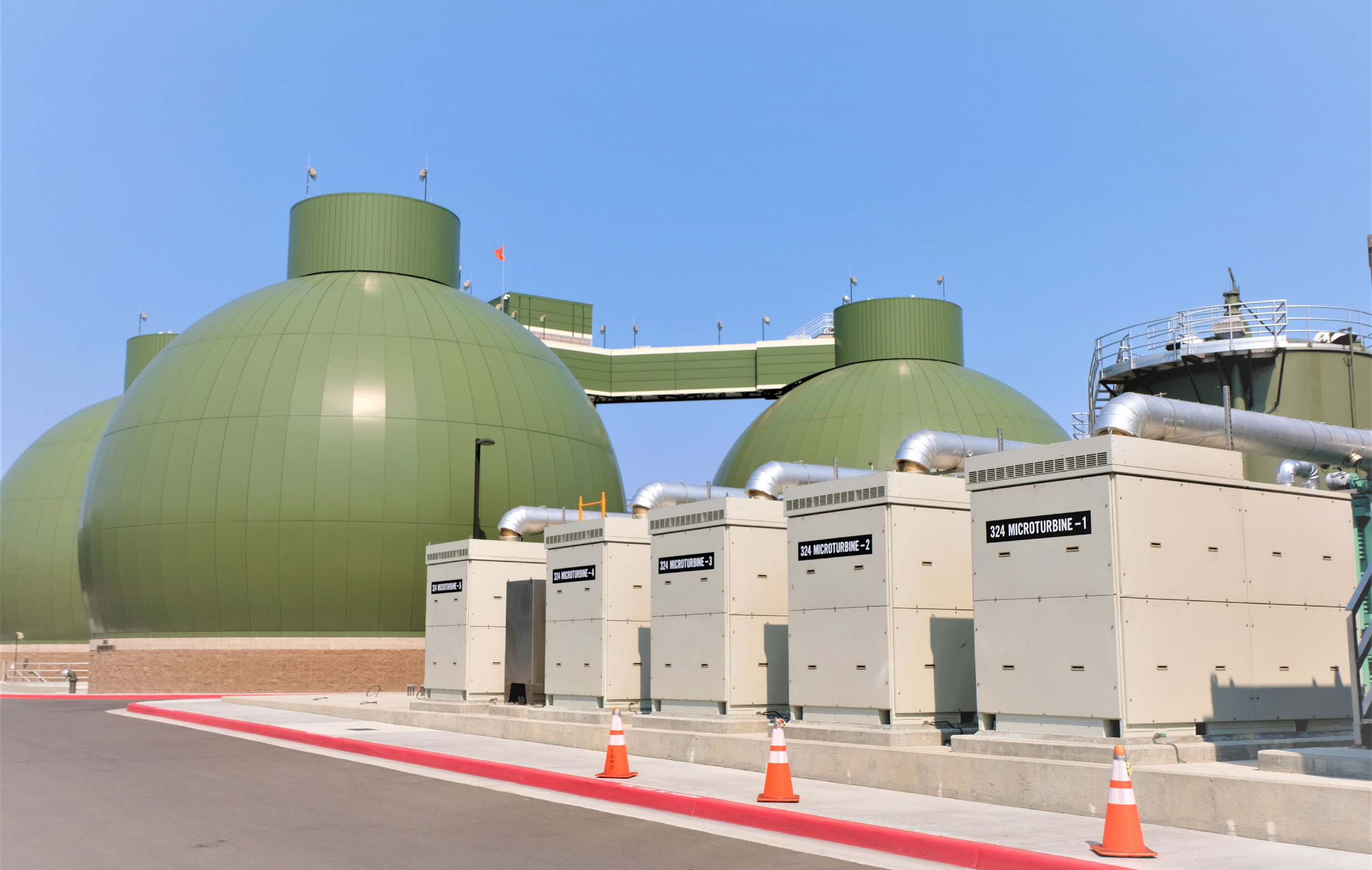 |
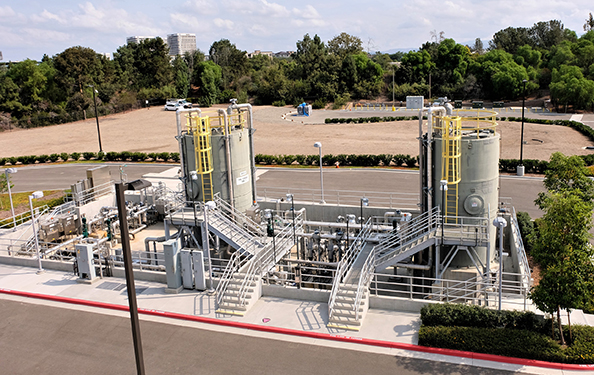 |
Digester gas is used on site to power the microturbine system. Each microturbine is rated for up to 200 kw, and the waste heat from the system is directed to an exhaust heat exchanger where the heat is transferred to the digester heating water system.
|
Fats, oil, and grease (FOG) receiving station: The facility’s trucked-in FOG receiving station consists of receiving pumps, two cone-bottom holding tanks, FOG recirculation and heating equipment, and a unique metering system for blending FOG with digested sludge to feed to the digesters.
|
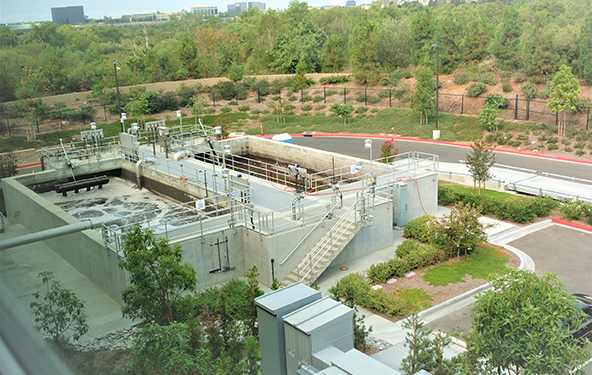 |
|
Dewatering centrate treatment sequencing batch reactors (SBRs): Centrate from the dewatering process is treated in two SBRs to reduce ammonia and remove residual solids prior to being returned to the liquids treatment process. Each tank uses fine-bubble diffusion for aeration and a tilting weir to decant treated centrate from the tanks.
|
|
|